
Progress in grinding performance by additive manufacturing of
Additive manufactured grinding tool Vat photopolymerization Cooling channels 1. Introduction Resin-bonded grinding wheels containing different types of In This paper an experimental studying for manufacturing grinding wheels from)) with particle 3 O 2 different abrasive materials (silicon carbide (SiC) and alumina (Al size (154µm)) and vitrified...(PDF) Study Some Properties for Manufactured Grinding
احصل على السعر
Manufacturing Miniature Products by Micro-grinding: A
In the recent years, a number of micro-manufacturing processes have been developed to produce such miniature and complex structures. Micro-grinding is one grinding machine, tool that employs a rotating abrasive wheel to change the shape or dimensions of a hard, usually metallic, body. All of the many types of grinding machines use a grinding wheel made from one of the Grinding machine Grinding Wheels, Abrasives, Precision
احصل على السعر
Chapter 16: Grinding Wheels and Operations American
Manufactured diamonds are now used for grinding tough and very hard steels, cemented carbide and aluminum oxide cutting tools. Abrasive grains are held together in a grinding wheel by a bonding material. The In this study, a process strategy for finishing copper surfaces with batch-manufactured micro-grinding tools in an electrochemically assisted grinding process is Detailed characterisation of batch-manufactured flexible micro
احصل على السعر
Additive manufacturing of metal-bonded grinding tools
Grinding tools with superabrasive grains can be manufactured from different bond materials. In several industrial applications, metallic bond systems are Surface grinding experiments with different cutting parameters were carried out to evaluate the grinding efficiency of the additive manufactured grinding wheels, and the results are summarized below. In deep grinding experiments and at constant cutting parameters, the observed wear of the grinding wheel with cooling Digital light processing-based additive manufacturing of resin
احصل على السعر
Manufacturing Miniature Products by Micro-grinding: A Review
A Nano-grinding centre as shown in Fig. 2 (a) developed by Aurich et al. was used to integrate the fabrication of micro-pencil grinding tool and perform the micro-grinding of silicon [1]. Dimension of the machine was 900×600×600 mm and it could provide a wide speed range of 15,000 to 160,000 rpm.Most used abrasives in an industry are artificial. Alumina is used in most grinding operations, and is mainly used in the grinding operation of ferrous metals. Also, ceramic is mostly used as manufactured abrasive to grind hard brittle metals. Other abrasive material is silicon carbide which used to grind high density materials andStudy Some Properties for Manufactured Grinding Wheels by Use
احصل على السعر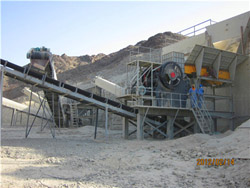
Precision Grinding: All Need To Know in Grinding Machining
Precision grinding is a form of grinding process that focuses on manufacturing and finishing parts with very close tolerances. Typically, grinding machining constitutes a subset of cutting as a metal-cutting process in manufacturing and tool-making. In production, grinding is used for machining various materials, particularly for making The mechanical 2 (0.088 g/cm and physical properties improve with increasing the vitrified bond percentage for manufacturing grinding wheels from different abrasive materials, also the strength values of manufactured samples from alumina (Al2O3) higher than that of manufactured samples from silicon carbide (SiC).Review of Dressing and Truing Operations for Grinding Wheels
احصل على السعر
Energy-Efficient Advanced Ultrafine Grinding of Particles Using
The present literature review explores the energy-efficient ultrafine grinding of particles using stirred mills. The review provides an overview of the different techniques for size reduction and the impact of energy requirements on the choice of stirred mills. It also discusses the factors, including the design, operating parameters, and feed This being the case, the costs and risks related to the use of grinding fluids must be taken into account in the operation design. Together with the cost of the fluid itself, other aspects must also be analyzed and manufactured. Grinding experiments show that improvements in wheel life and surface finish are possible using theStrategies for optimal use of fluids in grinding ScienceDirect
احصل على السعر
Grinding Wheel an overview ScienceDirect Topics
Grinding and finishing processes. Mark J. Jackson, in Modern Machining Technology, 2011 4.2.6 Modifications to the grinding process. When the grinding wheel and dressing wheel have been specified for a particular grinding operation, adjustments can be made during the dressing operation that affect the surface roughness condition of the grinding wheel. PRISMA flow diagram of the study selection process. Of the papers included for review, 27 were on abrasive grinding wheels with machined grooves, 24 were on engineered grooves, 18 were on laserTexturing Methods of Abrasive Grinding Wheels: A Systematic
احصل على السعر
Innovations in Abrasive Products for Precision Grinding
grinding. abrasives. machine. Innovations in Abrasive Products for Precision Grinding J. Webster (1), Saint Gobain Abrasives, USA M. Tricard (3), QED Technologies, USA Abstract This paper is a review of recent developments in the design and manufacture of precision, fixed-abrasive tools. The role of each component within 1. Introduction. Grinding is a typical precision machining technology, which is often used as the final process in part machining to ensure high dimensional accuracy and surface quality [1].As the main tool of grinding technology, grinding wheel is widely used in the precision machining of key parts in aerospace, automobile, ship, medical Pore morphology design and grinding performance evaluation of
احصل على السعر
Chapter 16: Grinding Wheels and Operations
Resinoid wheels are used for grinding speeds up to 16,500 SFPM. Their main use is in rough grinding and cut-off operations. This bonding material is used when heat generated by grinding must be kept to a minimum. Therefore, batch manufactured flexible micro-grinding tools are used for grinding of copper and oxidized copper surfaces to machine microstructure or local areas of functional surfaces.Detailed characterisation of batch-manufactured flexible micro-grinding
احصل على السعر
Modeling the costs and benefits of manufacturing expedient milling
An unshaped mano and unshaped grinding slab were also used in the grinding experiments. Dimensions for all grinding slabs and manos are listed in Table 1. Most grinding surfaces were manufactured using a combination of power tools and stone tools, though grinding slab #3 and mano #3 were made entirely with stone tools.Best overall coffee grinder: Fellow Opus Grinder, £188.95. Best coffee grinder for speedy results: De'Longhi Dedica Style KG521.M, £162.99. Best coffee grinder for versatility: KitchenAid Coffee Grinder 5KCG8433, £203.75. Best coffee grinder for ease of use: Gastroback 42642 Design Coffee Grinder Advanced Plus, £149.99.Best coffee grinders 2023 electric and hand-held BBC Good
احصل على السعر
(PDF) Study Some Properties for Manufactured Grinding Wheels by Use
Australian Journal of Basic and Applied Sciences, 11(2) February 2017, Pages: 50-58 AUSTRALIAN JOURNAL OF BASIC AND APPLIED SCIENCES ISSN:1991-8178 EISSN: 2309-8414 Journal home page: ajbasweb Study Some Properties for Manufactured Grinding Wheels by Use Different Abrasive Materials 1 Hussein Talab Most (95%) of the millers use locally manufactured grinding plates. Food and feed items that could form part of the milling processes were cassava, fish, groundnut, soya beans, cow-pea, and paddyThe quality of locally-manufactured cornmill grinding plates
احصل على السعر
Texturing Methods of Abrasive Grinding Wheels: A Systematic
1. Introduction. Abrasive grinding wheels are widely used in industry for the roughing and surface finishing of components through a chip-removal process [1,2].This requires very high cutting forces which, together with the friction between the tool and the workpiece to be worn, generate high amounts of heat [3,4].Excess heat can cause several problems, both Selective laser melted Ti-6Al-4V workpiece was used in grinding. Layer by layer deposited additively manufactured products are highly anisotropic in their properties (Liu et al. 2019).They also possess high residual stress (Heigel et al. 2018).To avoid the effect of these on grinding, the SLM samples were heat-treated for 4 h at 800° Superabrasive Grinding Characteristics of Additively Manufactured Ti
احصل على السعر
Qualification of the Low-pressure Cold Gas Spraying for the
Grinding wheels are usually manufactured by powder metallurgical processes, i.e., by molding and sintering. Since this requires the production of special molds and the sintering is typically carried out in a continuous furnace, this process is time-consuming and cost-intensive. Therefore, it is only worthwhile for medium and large
احصل على السعر