
Operational parameters affecting the vertical roller mill
Effect of table speed on product rate is given in detail in Fig. 5. With increasing table rpm at constant classifier rpm more ore is transported into the grinding gap and hence more ore is ground in the same time. The product particle size increases from Grinding and separation efficiency of vertical roller mill were evaluated. In addition to these, performance figures of vertical (PDF) Performance Evaluation of Vertical Roller Mill in
احصل على السعر
Operational parameters affecting the vertical roller mill
Generally, the plant operator can control the classifier cut size, and thus the comminuted product fineness by adjusting the classifier rotor speed, dam ring height, In the study the advantages of vertical roller mill are discussed over ball mills. VRM construction, its process and parameters which affects the performance and Review on vertical roller mill in cement industry & its
احصل على السعر
Operational parameters affecting the vertical roller mill
The classifier performance has a significant effect on this improvement of VRM grinding efficiency. The classifier reject material creates coarser material bed on The Vertical Roller Mill (VRM) reduces the power consumption for cement grinding approximately 30-40% associated with other grinding mills. The process variables in PROCESS CONTROL FOR CEMENT GRINDING IN VERTICAL
احصل على السعر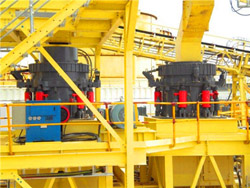
Analysis of vertical roller mill performance with changes in material
The vertical roller mill (VRM) is commonly used for secondary and tertiary crushing processes in numerous industries. In this study, the discrete element The feeding effect of the screw conveyor can be adjusted by changing the blade shape, screw rotational speed or screw length, etc (Kretz et al., 2016).In this Effect of the rotational speeds of the screw conveyor and milling
احصل على السعر
Modelling of pilot scale vertical roller mill operated in overflow
Vertical roller mill was separated into the two section as grinding and separation. Grinding operation was defined by population balance model and breakage rate was correlated Roller mills are commonly referred to by the type of service they perform. A mill used to crack grain or other types of friable materials may be called a cracking mill. Mills used to flake grains or other products may be called flaking mills or flakers. Roller mills used to grind in a feed mill are commonly referred to as a roller mill oreffect of table speed in vertical roller mill
احصل على السعر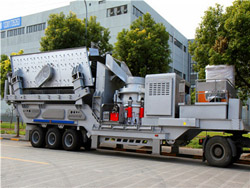
Analysis of Flow Field in Vertical Roller Mill Chamber Based on
Research on the 3-D Two-Phase Turbulent Flow Field in the Chamber of Vertical Roller Mill. Zhou Yiqi. Engineering, Physics. 2009. A 3-D chamber model of HRM4800 was established by use of SolidWorks.According to operation data of the chamber,the turbulent characteristic of the flow field and the boundary parameters of The application of vertical-roller-mills (VRM’s) for ore grinding is part of the second strategy. The grinding parts of a Loesche mill ( Fig. 1) are a rotating table (1) with a horizontal grinding track and rollers (2), which are pressed onto the table by lever arms and a hydro pneumatic spring system.Research of iron ore grinding in a vertical-roller-mill
احصل على السعر
Efficient machine learning model to predict fineness, in a vertical
β [1 − α; p 2; n − p − 1 2] = (1–α) th quantile of β [p 2; n − p − 1 2] distribution. For α = 0.05, the number of outliers is 44 among 280 data corresponding to an upper limit control U C L M a h a l a n o b i s = 4.55 as illustrated in Fig. 3.The results of these outliers have been carefully analyzed by a process expert from the cement plant. The unstable vibration of the roller mill is known to be self-excited and to have a fundamental frequency which differs from the frequency inherent to the mill operation. However, so far as conventional research is concerned, very few studies about this unstable vibration have been carried out and the generation mechanism has not Unstable vibration of roller mills ScienceDirect
احصل على السعر
Indicate Contributions from Several Radial VHYHQ4&WRROV
Increase productivity of vertical roller mill using seven QC tools Praveen Pareek1 and Dr. Vijayendra Singh Sankhla1 1 Department of Mechanical Engineering, GITS, Udaipur, India. Email: praveen.parieek@gmail Abstract. Cement sector in india is enjoyign success and capacity enhancement due to theAnalysis of vertical roller mill performance with changes in material properties and operating conditions using DEM. Author links open overlay (2019) discovered the effects of rotation speed and structure of crushing rolls on the performance of a toothed double-roll crusher. The results showed that when the roll’s speed wasAnalysis of vertical roller mill performance with changes in
احصل على السعر
Comparative analysis of conventional and fuzzy FMECA approach
The detailed FMEA of vertical roller mill presented in Table 2. To evaluate the criticality of the failure modes, S, O, and D criteria presented in Table 3,in which 1 signifies the least important of the risk parameter and 10 signifies the maximum importance of that risk parameter.Design parameters of vertical roller mill Table diameter (m) 4.6 Table speed M-roller (bar) 94 94 Classifier rotor speed (1/min) 108 111 Spec. power total (kwh/t) 28.74 29.85Performance Evaluation of Vertical Roller Mill in Cement
احصل على السعر
Review on vertical roller mill in cement industry & its
Vertical roller mill. The feed is ground by pressure and friction between the horizontal rotating table and 4 to 6 grinding rollers in the VRM. These rollers are hydraulically pressed against the table as shown in Fig. 3. To enhance grinding operation, the rollers and axes of the table should not move through the plane of the table. There is Productivity increase of the vertical roller mill for cement grinding. In Proceedings of the IEEE Cement Industry T echnical Conference, Hershey,P A, USA, 20–24 April 1997.Analysis and Optimization of Grinding Performance of Vertical Roller
احصل على السعر
Operational parameters affecting the vertical roller mill
Furthermore, VRM separator speed (rpm) is one of the key operational parameters that determines product particle size. Increasing the classi er rotor speed from 60 to 80 rpm decreases the particletable and is bited between the table and roller. It is then compressed and sheared for grinding. be obtained easily by changing revolving speed of the separator. The tyres and rollers can be replaced simply by Vertical Roller Mill 1. Rotary Lock 2. Separator 3. Chute 4. Roller 5. Swing Lever 6. Table 7.VERTICAL ROLLER MILLS AMCL
احصل على السعر
Energy-Efficient Technologies in Cement Grinding IntechOpen
The energy consumption of the total grinding plant can be reduced by 20–30 % for cement clinker and 30–40 % for other raw materials. The overall grinding circuit efficiency and stability are improved. The maintenance cost of the ball mill is reduced as the lifetime of grinding media and partition grates is extended. 2.5.1990. In order to reduce the larger pressure resistance (pressure difference between inlet and outlet) of a vertical roller mill, the flow field in the vertical roller mill is numerically simulated by CFD technology. Based on the simulation results, the reasons that led to the larger pressure resistance of the vertical roller mill is studiedNumerical Study of the Flow Field in a Vertical Roller Mill
احصل على السعر
Analysis of vertical roller mill performance with changes in
The vertical roller mill (VRM), (Johansson et al., 2017) used DEM to simulate a laboratory cone crusher to investigate the effects of speed and eccentricity on particle size distribution, power draw, and mass flow. Li et al. Table 3 gives the shape parameters of three meta-particles.The Institute of Mineral Processing at the Montanuniversitaet Leoben in cooperation with the company CEMTEC has developed a pilot scale, 200 mm table diameter, vertical roller mill for energy controlled laboratory tests. The mill provides the technical options to vary process parameters like air-flow, mass flow, grinding force and An energy based comparison of vertical roller mills and
احصل على السعر
Effects of rotation speed and rice sieve geometry on turbulent motion
DEM simulations were used to investigate the effects of rotation speed and cross-section shape of rice sieve in a vertical rice mill. The simulation results for the 8-sided regular polygon sieve at rotation speeds of 1400 rpm were first compared with experimental results using the dimensionless residence time distribution, and the results were in good of 80mm. The raw materials are mixed in a certain proportion and fed into a vertical roller mill (LOESCHE mill). The vertical roller mill grinds the marital to D 85 of 90µm. The ground product is calcined in a preheater to 850-900℃. After calcination, the materials enter to a rotary kiln and heated to 1450℃ to become clinker.Modeling and simulation of vertical roller mill using population
احصل على السعر
Vertical Roller Mills FLSmidth
It features a patented roller and table design and concrete mill stands instead of traditional, heavy steel structures. The OKTM Mill’s flexible design makes it possible to operate it with a number of rollers out of service while still reaching 60 to 70 percent of the normal operation output, minimising production losses.
احصل على السعر