
(PDF) Energy Efficient Ball Mill Circuit Equipment Sizing
The energy saving resulting from the replacement of cyclones with screens in a closed ball mill circuit was estimated to be in the range of 10 to 25% The measured Bond ball mill energy consumption in relation to mill revolution from the data of various ore types and feed sizes (Shi et al., 2006). A similar Comparison of energy efficiency between ball mills and
احصل على السعر
Calculation method and its application for energy
Measurement results of two ball mills in a real ceramic manufacturing plant showed that the proposed calculation models could achieve an accuracy of more than 96% for predicting Firstly, based on the material fatigue damage accumulation theory, the energy-saving mechanism of the planetary ball mill is analyzed, which shows that the Development of planetary mill and its energy-saving mechanism
احصل على السعر
Analysis of dynamic similarity and energy-saving
Thus, we simplified the process of ball motion between its detachment and subsequent reattachment to the vial wall. Considering that the value of t 2 is relatively • Start with 75-100% of the maximal operation frequency of the ball mill. • The thermal stress for the reactants could be reduced by using cycled mode: mill for a specific Ball Milling in Organic Synthesis: Solutions and Challanges
احصل على السعر
Modeling and Analysis of High-Energy Ball Milling Through Attritors
In this study, we have focused on the investigation of the effects of major controllable processing parameters of attritor mills to provide guidance in the selection of To evaluate the net energy consumption of the stirred mill, the specific energy input [26,27] E m (kWh /t) was calculated as follows: E m = ∫ P t − P 0 dt m Where P(t) is the mean power of the stirred mill at each sampling time, kW; P 0 is the mean power of the stirred mill under no load (no water, grinding media and material), kW; t is grinding Impact of ball filling rate and stirrer tip speed on milling iron ore
احصل على السعر
Energy and exergy analyses for a cement ball mill of a new
Nowadays, ball mills are used widely in cement plants to grind clinker and gypsum to produce cement. In this work, the energy and exergy analyses of a cement ball mill (CBM) were performed and some measurements were carried out in an existing CBM in a cement plant to improve the efficiency of the grinding process. The first and second Quality of the powders. The quality of a powder can be described by a set of indicators corresponding to ‘good’ and predictable properties. In this study, good powder properties would mean low span, high specific surface, low elongation, little agglomeration, low compressibility and weak cohesion.Properties of biomass powders resulting from Open
احصل على السعر
Ball Mill an overview ScienceDirect Topics
A feature of ball mills is their high specific energy consumption. A mill filled with balls, working idle, consumes approximately as much energy as at full-scale capacity, that is, during the grinding of material. Therefore, it is most disadvantageous to use a ball mill at less than full capacity.@article{osti_922135, title = {Improving Energy Efficiency Via Optimized Charge Motion and Slurry Flow in Plant Scale Sag Mills}, author = {Rajamani, Raj K}, abstractNote = {A research team from the University of Utah is working to make inroads into saving energy in these SAG mills. In 2003, Industries of the Future Program of the Improving Energy Efficiency Via Optimized Charge Motion and
احصل على السعر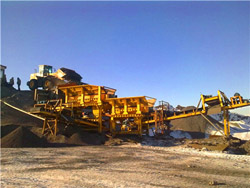
Measurement of electrical energy consumption in a Bond ball mill
Abstract and Figures. In this paper a new digital energy meter is being evaluated as a means of measuring the energy required to grind ore in the Bond mill and to test if the results areOne of the most used tumbling mills is the ball mill. This paper reviews different types of grinding media that have been developed and improved over the years and their properties. Also reviewed(PDF) Grinding Media in Ball Mills-A Review ResearchGate
احصل على السعر
Milling Energy an overview ScienceDirect Topics
Ball milling is a mechanical process and thus all the structural and chemical changes are produced by mechanical energy.100 Baek et al. 101 recently proposed that edge-selectively functionalized graphene nanoplatelets (EFGnPs) as metal-free electrocatalysts for ORR can be large-scaled prepared by ball-milling method.Abstract. Discrete element (DE) simulation of a ball mill with a large number of particles is challenging when each particle is considered. Similarity principle could be adopted to reduce the number of particles in a simulation whilst still maintaining the accurate flow behaviour of particles. This paper presents a scaling relationship Discrete element simulation of particle motion in ball mills
احصل على السعر
Grinding Media in Ball Mills-A Review Preprints
flow inside the mill, showed that the collision energy of grinding media increased with mill speed from 22 to 45rpm giving more undersized product of 15.2mm, 11.2mm and 8.6mm and suddenly dropped when the mill was run at 67rpm. This therefore suggests that the ball mill should be run within its optimum range in this case, which is Milling was then performed in 80% ethanol for 30–120 minutes using a high-energy ball mill. The mechanical treatment resulted in a reduction of the fibre length and diameter, probably due to degradation of the cellulose Ball milling: a green technology for the preparation
احصل على السعر
Kinetic Energy Dose as a Unified Metric for Comparing Ball Mills
Mechanochemistry utilizes mechanical forces to activate chemical bonds. It offers environmentally benign routes for both (bio) organic and inorganic syntheses. However, direct comparison of mechanochemistry results is often very challenging. In mechanochemical synthetic protocols, ball mill setup (mechanical design and grinding A ball mill, a type of grinder, is a cylindrical device used in grinding (or mixing) materials like ores, chemicals, ceramic raw materials and paints. Ball mills rotate around a horizontal axis, partially filled with the material to be ground plus the grinding medium. Different materials are used as media, including ceramic balls, flint pebblesBall mill
احصل على السعر
Direct Mechanocatalysis: Using Milling Balls as Catalysts
Besides the mill geometries there exist several easy to control and reasonably well‐understood parameters unique to mechanochemical reactions. As mentioned above, the rotational speed (planetary ball mill) or milling frequency (vibrational ball mill) are an easy to adjust parameter to control the energy input in the milled powder.Angewandte Chemie int. ed., 15. Oktober 2021. Mechanocatalysis in a ball mill makes it possible to synthesise ammonia at much lower temperatures and pressures than those required for the Haber-Bosch process. This has been observed by a research team led by F. Schüth and S. Reichle from the Max-Planck-Institut für Ammonia synthesis by mechanocatalysis in a ball mill Max
احصل على السعر
Design, Construction, and Operation of a High-Energy Mill for
A high-energy mill was designed and built with the purpose of processing magnesium (Mg) powders. The main characteristics of the mill are grinding capacity of 1 kg and demolition elements of 10 kg; it has a distributed form to the interior ten blades of similar geometry, six of which are of the same size and four of them were increased in length in To really choose, I guess it depends on the material and your mill (vial, RPM, media, filling volume). I.e. Si80Ge20 is easily alloyed in the high energy SPEX mill.Best way to determine the ball-to-powder ratio in ball-milling?
احصل على السعر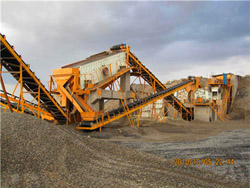
Effects of Ball Milling Processing Conditions and Alloy
1. Introduction. Mechanical alloying (MA) is a well-known way in processing advanced materials involving repeated welding and fracturing the powder particles in a high energy ball mill [1,2].First developed by Benjamin and his co-workers in 1970s [3,4], this processing method has been shown the potential in synthesizing Schönert (1988) estimated that replacing existing circuits with HPGR-ball mill circuits could increase circuit capacity by 12–25%, and reduce energy by 10–20%. However, for this to be achieved the HPGR must produce at least 10% of the final circuit product and, furthermore, damage those particles remaining unbroken.Improved characterisation of ball milling energy requirements for
احصل على السعر
Helping to reduce mining industry carbon emissions: A step-by
W bm = Overall ball mill net specific energy (kWh/t) K hpgr = Factor to account for weakening of ball mill feed by the HPGR (typically in the range 0.93–0.95) W a = Net specific energy to grind from ball mill feed to 750 μm. W b = Net specific energy to grind from 750 μm to ball mill circuit product. 4.3.1.1. Determination of the M ib parameter
احصل على السعر