
Experimental investigations and modelling of the ball
Due to their high energy density planetary ball mills are especially suited for fine and ultra-fine grinding of hard and brittle material down to the nanometre Based on the latest achievements in the literature, this review will: (a) delineate the principles and fundamentals for biochar ball milling; (b) evaluate the Ball milling as a mechanochemical technology for
احصل على السعر
Ball mill abrasion test (BMAT): Method development and
Introduction. The ball mill abrasion test (BMAT) is an industrially-relevant multipurpose wear test method that enables tribologists and abrasion scientists to study the abrasive wear behaviour of materials for various service applications, particularly for grinding balls and mill liners, under conditions and contact mechanics very similar to the The experiments were conducted as per Taguchi’s L9 orthogonal array. Preparation of magnetite nanoparticles by high-energy planetary ball mill and its application for ciprofloxacin degradation through heterogeneous Fenton process. Journal of Environmental Management, 211, 53–62. Article Google ScholarComparative Study on Improving the Ball Mill Process Parameters
احصل على السعر
IOP Conference Series: Earth and Environmental Science
The details specification of the ball mills can be found elsewhere [3]. The ball mill was utilized stainless steel balls with different sizes, i.e., 4.5 cm, 3.6 cm, and 2.4 cm diameter, with a mass ratio of 1:2:4, respectively. The mass ratio between the crab shell and the balls was 1:10, the combination of crab shell and the ball's volume isThe secondary ball mill can increase the surface area by reducing the with a speed of 86 r/min and a cylinder volume of 2.5 L (D × L = 140 mm × 160 mm). The amount of ore fed into the mill for each experiment was In industrial applications, the secondary ball mill can increase the surface area by reducing theEffect of Intensive Abrasion Breakage on Secondary Ball Mills
احصل على السعر
Energy Efficiency Analysis of Copper Ore Ball Mill Drive
Analysis of Variant Ball Mill Drive Systems. The basic element of a ball mill is the drum, in which the milling process takes place ( Figure 1 ). The length of the drum in the analyzed mill (without the lining) is 3.6 m, and the internal diameter is 3.4 m. The mass of the drum without the grinding media is 84 Mg.Research Highlights No considerable influence of speed ratio k in the range − 3 < k < − 1 on the grinding ball motion pattern was observed. Grinding ball motion is strongly affected by the friction arising, among others, from different feed materials. Friction necessarily has to be considered in studies on stress conditions in the planetary Experimental investigations and modelling of the ball motion in
احصل على السعر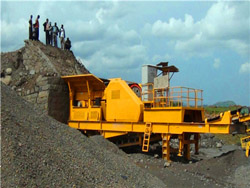
Recent advances in the treatment of contaminated soils by ball
This review is expected to promote the application and its in-depth research of ball milling technology on soil remediation. Graphical Ball mill is an excellent immobilization technique. The results of column experiments indicated that its Cr(VI) removal capacity was 0.54 mg/g, 0.39 mg/g and 0.29 mg/g at pH 5, 7Planetary ball mills are well known and used for particle size reduction on laboratory and pilot scales for decades while during the last few years the application of planetary ball mills has extended to mechanochemical approaches. Processes inside planetary ball mills are complex and strongly depen Process engineering with planetary ball mills PubMed
احصل على السعر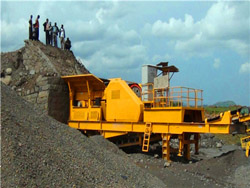
(PDF) Rod Mill Product Control and Its Relation to ResearchGate
Experimental design of the rod mill experiments for modeling purposes. Vc is the critical rotational speed of the mill, the solid feed is 3 kg/min, rod diameter 30 mm, and lifter height 23 mm. +4conditions and with different types of mills, such as high (or low) energy, centrifugal type, attritor type, vibratory type, and tumbling type. In the vibratory type of ball mill, grinding of the materials can be performed with vibratory motions with high frequencies and low amplitudes. The ball’s velocity in theRecent Developments on the Synthesis of Nanocomposite
احصل على السعر
Effect of mill type on the size reduction and phase transformation of
Single ball milling (TY) was carried out using a Retsch MM200 vibratory single ball mill. An 11 ml stainless steel milling jar with a 12 mm diameter spherical stainless steel ball is used for single ball milling for durations of up to 1200 min at a milling frequency of 30 Hz.In single ball milling (Fig. 2 a), short duration collisions dominate and the energy Ball milling is a simple, fast, cost-effective green technology with enormous potential. One of the most interesting applications of this technology in the field of cellulose is the preparation and the chemical modification of cellulose nanocrystals and nanofibers. Although a number of studies have been repo Recent Review Articles Nanoscale Ball milling: a green technology for the preparation and
احصل على السعر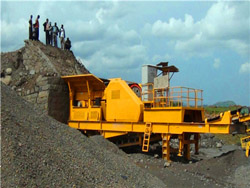
Ball milling as a synthesis method Aalto University Wiki
Introduction Ball milling is generally known as a method to mix, blend, shape and reduce particle sizes. It can also be used as a mechanical synthesis method to produce materials that are milled to extremely fine powders. Several factors, like milling temperature, type of mill, milling speed etc. need to be considered when using ball The ball filling ratio, φGB = grinding ball bulk volume / grinding chamber volume, was set to 0.3 for the standard case. In one set of experiments the filling ratio was increased up to a value of 0.7 in order to prove its influence on the ball motion. The varied parameters were studied without mill feed in a first step.Experimental investigations and modelling of the ball motion
احصل على السعر
A novel approach of evaluating crushing energy in ball mills
Introduction. Ball mill is a kind of widely used engineering machinery with low working efficiency [1,2]. Since the advent of the ball mill, researches on its grinding performance mainly aimed at the aspects of fill rate, rotational speed, ratio of steel balls, ratio of grinding medium and abrasive, number of lifter bars, the shape of lifter bars [3,5].Planetary ball mills are well known and used for particle size reduction on laboratory and pilot scales for decades while during the last few years the application of planetary ball mills has(PDF) Process Engineering with Planetary Ball Mills
احصل على السعر
Optimization of Solids Concentration in Iron Ore Ball Milling
Important advances have been made in the last 60 years or so in the modeling of ball mills using mathematical formulas and models. One approach that has gained popularity is the population balance model, in particular, when coupled to the specific breakage rate function. The paper demonstrates the application of this methodology to This paper presents a solution for the detection and control of coal loads that is more accurate and convenient than those currently used. To date, no research has addressed the use of a grinding medium as the controlled parameter. To improve the accuracy of the coal load detection based on the kinetic energy of balls in a tubular ball Energies Free Full-Text Modeling on the Effect of Coal Loads
احصل على السعر
Modeling ball impact on the wet mill liners and its application in
Various scenarios are simulated and results are used to predict the performance of magnetic mill liners in various ball mill applications. Introduction. In a (and levels) in a full factorial design, totaling 8 experiments (level factor = 2³). The tests were carried out in a mill of 148 L capacity, with a load of 87The ball mill Ball milling is a mechanical technique widely used to grind powders into ne particles and blend materials.18 Being an environmentally-friendly, cost-effective technique, it has found wide application in industry all over the world. Since this mini-review mainly focuses on the conditions applied for the prep-Ball milling: a green technology for the preparation and
احصل على السعر