
Fire Refining of Rough Antimony from Impurities for
A method for fire refining of rough antimony in an induction furnace was also developed. Here, the extraction of antimony into refined product comprises 84.2% with PDF A new generation of industrial induction melting furnaces has been developed during the last 25 years. Present practices (PDF) Induction Furnace -A Review ResearchGate
احصل على السعر
Effects of induction furnace conditions on lining refractory
A two-dimensional axisymmetric model based on the structure of the real induction melting furnace is constructed, electromagnetism, heat transfer, laminar flow The removal of harmful, volatile trace elements, such as antimony, tellurium, selenium and bismuth, in vacuum induction furnaces is of considerable Vacuum Induction Melting for Investment Casting
احصل على السعر
Melting and Crystal Growth in Induction Furnaces MDPI
Melt growth of crystals is undoubtedly the most popular method of growing large single crystals at relatively high growth rates. Mostly, functional crystals are Electromagnetic forces are used for induction melting of aluminum, in particular for scrap melting [1]. In this application, a molten heel is often used and the Modeling of Inclusion Behavior in an Aluminum
احصل على السعر
Metals Free Full-Text Study of the Influence of the Thermal
The thermal stability of the melting furnace is estimated by the number of melts, and each melting (in the case of a 2.5 t furnace) is the heating of the lining after UDC 669.187.2. Recently the use of induction furnaces has been increasing both high-quality metallurgy and in the manu- facture of intricate-shape Melting in induction furnaces with an acid lining Springer
احصل على السعر
Chromium Losses during Melting of Complex Nickel
loss upon melting ZhS26 and ZhS32 alloys in a vacuum induction furnace (heat mass of 10 kg): T m = (1) 1550°C, (2) 1620°C, and (3) 1690°C. 1.4 1.2 1.0 0.8 0.6 Copper slag cover in induction furnace (left), Al-chip melting in rotary furnace with salt slag (right) Filtration mechanisms in ceramic foam filters Filtration. In 1935 a procedure was proposed(PDF) Melt Treatment of Copper and Aluminium
احصل على السعر
(PDF) Mechanisms of graphite crucible
SEM micrographs of the graphite sample submerged into Si melt at 1500 C and held for 5 min, (a-c): vertical view to the surface of the graphite sample (d,e): the cross-section of the submergedThe main purpose of meltings the antimony raw materials is the transfer of the main substance of ore antimony in a less contaminated by iron metal. Durcrudeing melting, sulfides react with iron, forming sulphurous iron and metallic antimony, droplets of which collect on the bottom of the furnace, and the empty rock is slagged.Melting of crude antimony in the low-tonnage production
احصل على السعر
Research of the evaporation law of elemental antimony
The variation of the weight of elemental antimony with time is measured by a vacuum differential weight furnace, and the evaporation rate of elemental antimony is obtained by mathematical statistical analysis at temperatures of 973–1473 K and ambient pressures of 5–500 Pa. The experimental results show that: when the temperature is supplied during melting, antimony should predom-inantly occur as SbIII. Noble metals, such as silver, gold, or platinum occur in glasses and melt as metals or in an oxidized 1,300 to 1,400 C in an induction furnace using a Pt-crucible. Afterward, the glass melt was stirred for 1.5 to 2.0 h using a rotation frequency of up to 100 min-1Noble metals Pt, Au, and Ag as nucleating agents in
احصل على السعر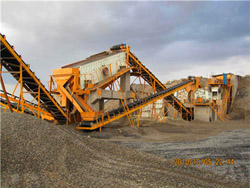
Loss of aluminium during the process of Ti-Al-V alloy
A research on kinetics of Al evaporation from liquid U–Al alloys was made in a vacuum induction melting (VIM) furnace at 1673–1843 K. The evaporation rate of Al was found to be first orderThe thermal stability of the melting furnace is estimated by the number of melts, and each melting (in the case of a 2.5 t furnace) is the heating of the lining after sintering to 1550 °C, then the melting mode occurs at 1550–1600 °C, and the temperature drops to 1450–1470 °C to drain the first portion of the alloy.Metals Free Full-Text Study of the Influence of the Thermal
احصل على السعر
(PDF) Induction Furnace -A Review ResearchGate
Abstract and Figures. A new generation of industrial induction melting furnaces has been developed during the last 25 years. Present practices followed in Induction Furnaces are discussed in thisIn Quartzrial Induction Melting Furnace For Platinum. Gold Melting Furnace CE Approved Gold Smelting Machine . A mini induction furnace is a small kiln with high power specifically designed andmanufactured for melting of precious metals like gold silver platinum etc. our miniinduction furnace costs about $900 as they are safer to use andmelting antimony in a induction furnace
احصل على السعر
Study on the behavior of impurities in zone melting of
The calculation model established a three-dimensional geometric model according to at 1:1 melting furnace in the actual area. This simulation did not produce additional results, but laid the foundation for the numerical simulation method to study the zone melting of the Al. Download : Download high-res image (100KB) Download : Atomized ferrosilicon is produced by melting high-grade crude FeSi-75 (75% Si and 25% Fe) and diluting it with low-carbon steel scrap in an induction furnace until the silicon content of the melt is 15% and the iron content 85%. Atomization can be done using either a steam jet or inert gas jets (Collins, Napier-Munn, and Sciarone, 1974).Accretion formation on the refractory lining during the melting
احصل على السعر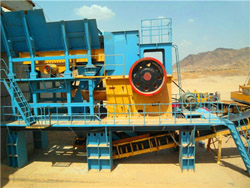
Analysis of Antimony Sulfide Oxidation Mechanism in
Antimony is considered an important metal, and various antimony compounds are widely used in electronics, flame retardants, chemicals, alloys, and semiconductor materials. 1 Antimony exists mainly in the form of antimony sulfide, which is usually smelted by volatilization in the blast furnace. However, the process has some As antimony is typically present in industrial and commercial products only in small amounts, the concentration of antimony in waste types is low and a limited amount of antimony is currently recycled. One product relatively rich in antimony is the metal oxide varistor (MOV) used for overvoltage protection in electric circuits. To increase the Recovery of Antimony: A Laboratory Study on the Thermal
احصل على السعر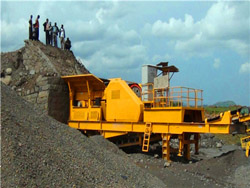
Effect of Antimony on Graphite Growth in Ductile Iron
Furthermore, a ductile cast iron melt was prepared. The base melt, consisting of pig iron, ductile iron returns and steel scrap, was melted in a medium frequency induction furnace with a melt capacity of 35 kg. FeSi75 and graphite were added to reach the target chemical composition. The melt was treated at 1505 °C with a Mg-containing 1 天前SuperbMelt electric induction melting furnace can melt different kinds of metals under the condition of using the same furnace, which reduces the time and cost of replacing the furnace and saves a lot of money. 0.5 per cent copper and 0.3 per cent antimony. After floatation parting, the concentrate would consist of 1.7 per cent silver, 10Silver Melting Furnace, Electric Silver Smelting Furnace for Sale
احصل على السعر
Selecting the Right Unit for Efficient Induction Melting
The stirring action in a properly sized induction furnace produces a homogeneous melt without gas pickup, refractory inclusions or alloy loss. Melting times can and should be exceedingly fast. Typical recommended melting times for iron are as follows: 300-500 lbs. in about 22 minutes; 750 lbs. in about 27 minutes; 1,000 lbs. in about 36 minutes.The polytherms of the surface tension of these melts have a linear character, the removal of antimony from the Fe–Sb–Al2O3 melts depends on the time of melting in a vacuum induction furnace(PDF) Modeling of Material and Heat Balance of
احصل على السعر
What is VIM + ESR? Introducing the Smelting Method of
Induction furnaces generate heat through electromagnetic induction, which is then used to melt metals. Induction furnaces have the following features: 1. Induction furnaces use electromagnetic induction heating to melt metals. There is no metal contact with the heating element during the smelting process. It does not require carbon as an
احصل على السعر