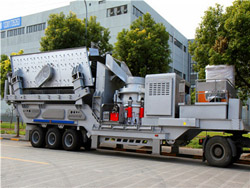
Dry Process Of Cement Manufacturing Dry Cement
The new dry-process of cement manufacturing technology makes good use of the limestone resources discarded in the traditional mining method and applies the pre decomposition technology, suspension preheating Raw Materials processing included: Setting and curing and cement manufacturing process,Process Discretion: Wet process, Semi-dry process, Dry process and Finish process.(PDF) Cement Manufacturing ResearchGate
احصل على السعر
Manufacture of Portland Cement- Materials and Process
8 行Fig: Manufacture of Cement by Dry Process. b) Wet Process The raw materials are firstlyAlthough the dry process is the most modern and popular way to manufacture cement, some kilns in the United States use a wet process. The two processes are essentially alike except in the wet process, the How Cement Is Made
احصل على السعر
Dry process cement Britannica
In cement: Manufacture of cement are known as the wet, dry, and semidry processes and are so termed when the raw materials are ground wet and fed to the kiln as a slurry, Methods of cement manufacturing 1- Wet process : grinding and mixing of the raw materials in the existence of water. 2- Dry process : grinding and mixing of the raw Methods of cement manufacturing General Manufacturing Process
احصل على السعر
How Cement is Made Cement Manufacturing Process Civil
Stage of Cement Manufacture. There are six main stages of the cement manufacturing process. Stage 1: Raw Material Extraction/Quarry The raw cement ingredients needed for cement production are limestone (calcium), sand and clay (silicon, aluminum, iron), shale, fly ash, mill scale, and bauxite. The ore rocks are quarried and crushed into smaller Semi-dry Process of Cement Manufacturing. The blended meal will be sieved and then fed into the rotating dish in a semi-dry process. It is known to us as the granulator. The water content in this Dry Process of Cement Manufacturing Semi-dry
احصل على السعر
Manufacture of rich-sulfoaluminate belite cement at low
This study, within the framework of eco-cement development, aims to manufacture reactive belite-sulfoaluminate cement (BYF) as alternative to Portland cement (PC). This ecological cement is obtained at low temperature from a mixture of industrial wastes using two synthetic methods, dry and hydrothermal treatment.Manufacturing of cement is a process that involves several steps, from extracting raw materials to packaging and shipping the final product. In this blog post, we will explain two main processes of cement manufacturing and how they affect the quality and properties of cement. The wet process and the dry process are the two primary ways that2 Types of Manufacturing of Cement Wet and Dry Process
احصل على السعر
(PDF) THE CEMENT MANUFACTURING PROCESS Academia.edu
They are mixed either dry (dry mixing) or by water (wet mixing). 3) Prepared raw mix is fed into the rotary kiln. 4) As the materials pass through the kiln their temperature is rised upto 1300-1600 °C. The process of heating is named as “burning”. The output is known as “clinker” which is 0.15-5 cm in diameter. 5) Clinker is cooledCement is so fine that 1 pound of cement contains 150 billion grains. The cement is now ready for transport to ready-mix concrete companies to be used in a variety of construction projects. Although the dry process is the most modern and popular way to manufacture cement, some kilns in the United States use a wet process.How Cement Is Made
احصل على السعر
What is the manufacturing process of Portland Cement?
In these animated video you can see WET and DRY process in Cement Manufacturing and another video about Cement Production’s simulation at one of cement factories. In 2nd video you can see full details of each section of manufacturing of Portland cement, one by one in 4 minutes briefly.Each bag of cement contains 50 kg or 0 m3 of cement. Figure 1. Flow Chart of Wet Process for manufacturing of cement. 1. Difference between Dry Process and Wet Process. If we consider the quality and rate then wet process is better and if we consider fuel consumption and time of process then dry process is better. D r y p r o c e s s W Cement Manufacturing: wet process and dry process Studocu
احصل على السعر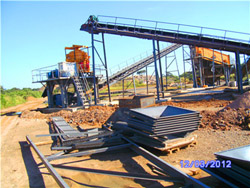
DETAILED DRY PROCESS OF CEMENT MANUFACTURING LCETED
In dry and semi-dry processes for the manufacture of cement, raw materials are crushed and fed into the grinder in the correct proportions. The raw material is dried and reduced in size to a fine powder in a grinder. Dry powder is called a raw meal. Raw meals are pumped into mixing silos. Adjustment of the proportions of materials required forIn this process, the raw materials are first reduce in size of about 25 mm in crushers. A current of dry air is then pass over these dry materials. These dry materials are then pulverise into fine powder ball mills and tube mills. All these operations are do separately for each raw material and they are store in hoppers.Manufacture of Portland Cement Process and Material use
احصل على السعر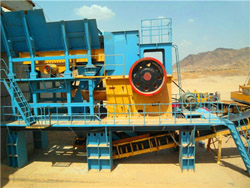
Manufacture Process Of Cement Step By Step
Manufacture process of cement. 1) Mixing of raw material:- A materials like as limestone or chalk and shale or clay may be mixed either in dry condition or wet condition. The process of according is known as dry Dry Process. Dry process method means manufacturing raw materials into raw materials powder, whose water content is generally less than 1%. So, the dry process can `reduces heat loss needed by heating and Why Choose Dry Process From Manufacturing
احصل على السعر
Cement Manufacture an overview ScienceDirect Topics
2. Cement Plants. Portland cement manufacture accounts for about 98% of the cement production in the United States. The raw materials are crushed, processed, proportioned, ground, and blended before going to the final process, which may be either wet or dry.The manufacture of Portland cement is a complex process and done in the following steps: grinding the raw materials, mixing them in certain proportions depending upon their purity and composition, and burning them to sintering in a kiln at a temperature of about 1350 to 1500 ⁰C. During this process, these materials partially fuse to form Manufacturing of Portland Cement Process and Materials
احصل على السعر
Manufacture Of Portland Cement Process Flow chart civil
Mixing of raw materials: The processes used for the manufacture of portland cement can be classified as dry and wet. In dry process. The raw materials are first reduced in size of about 25mm in crushers and Crushed material is ground to get fine particles into ball mill or tube mill. Each material after screening is stored in a separate 2. Cement Plants Portland cement manufacture accounts for about 98% of the cement production in the United States. The raw materials are crushed, processed, proportioned, ground, and blended before going to the final process, which may be either wet or dry.What Is Dry Process Of Cement? building materials
احصل على السعر
Manufacturing of Cement by Dry Process Search IndexBox
The dry process of cement manufacturing involves kiln firing of raw materials in dry state. The dry process consumes less energy and its running costs are lower than that of the wet process. Hoever, the dry process is not eco-friendly, due to the fact that it requires huge amounts of capital investment for machines and equipments.Manufacture of Portland cement Portland cement is essentially calcium silicate cement, which is produced by firing to partial fusion, There are two processes known as “wet” and “dry” processes depending upon whether the mixing and grinding of raw materials is done in wet or dry conditions. 2 1.Cements University of Babylon
احصل على السعر
Dry process cement Britannica
In cement: Manufacture of cement. are known as the wet, dry, and semidry processes and are so termed when the raw materials are ground wet and fed to the kiln as a slurry, ground dry and fed as a dry powder, or ground dry and then moistened to form nodules that are fed to the. Read More. Other articles where dry process is discussedCement is manufactured by integrating lime components and argillaceous components in a ratio of 3:1. Lime components can be limestone chalk, seashells, and marl while argillaceous components can be shale clay, blast furnace slag, or slate. The lime component is used to obtain the component called lime while the argillaceous component isManufacturing of Cement Process Dry Process Wet Process
احصل على السعر