
Ball Mill Design/Power Calculation 911 Metallurgist
The basic parameters used in ball mill design (power calculations), rod mill or any tumbling mill sizing are; material to be The specific comminution energy for milling in the Bond test mill appears to be based on 60 J/rev, which defines the net energy Measurement of electrical energy consumption in a
احصل على السعر
Charge behaviour and power consumption in ball mills:
Typical power consumption for a 5-m diameter by 7-m-long ball mill is between 2.5 and 3.5 MW. The actual proportion of this energy usefully used in size The ball mill comminution process has a high electrical energy consumption, especially when those systems are in combination with first- or second-generation classifiers. This BALL MILLS Ball mill optimisation
احصل على السعر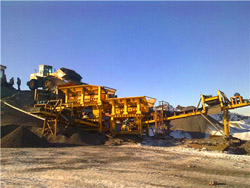
(PDF) Determination of granulometrical composition of the clinker
The energy consumption of grinding is the subject of many studies, especially in the case of ball mills for grinding clinkers [8, 9], fuels [10], iron ore [11], hematite ore [12], sulfide ore [13The approximate horsepower HP of a mill can be calculated from the following equation: HP = (W) (C) (Sin a) (2π) (N)/ 33000. where: W = weight of charge. C = distance of centre of gravity or charge Ball Mill Design/Power Calculation 911 Metallurgist
احصل على السعر
Analysis of the efficiency of the process in closed circuit ball mills
ball mill open and closed circuits [12] with the installation in all cases the dynamic separator. When transferring to closedcircuit а mill size 2.6×13 m at a constant quality cement (3000 cm2pg) capacity grinding unit was increased from 25 to 38 tph while reducing the specific consumption of electricity from 41.6 to 29.3 kWhpt. The parameterBall mills for fine grinding cement clinker and additives are specific consumption of electricity from 28.9 to 22. V.S. Bogdanov. Cement and its application. 6. 12 16 (1998) Jan 2015; 84-89;(PDF) Analysis of the efficiency of the grinding process in closed
احصل على السعر
A Survey and Analysis on Electricity Consumption of Raw Material Mill
A Survey and Analysis on Electricity Consumption of Raw Material Mill System in China Cement Industry between 2014 and 2019 material mill dropped from 30.88 kWh/t in 2014 to 16.13 kWh/t in 2019, with a drop of more than the diameter of the ball mill has reached 5 6 m,4% of global electric energy consumption [3–6]. In the United States, the milling process is estimated to account for 0.5% of the primary energy consumption, 3.8% of the total electric energy consumption, and 40% of the total energy consumption in the mining industry [7]. In Poland, the annual electric energy consumption from copper oreEnergy Efficiency Analysis of Copper Ore Ball Mill Drive Systems
احصل على السعر
(PDF) The Effects of Temperature, Vibration and Dosage on the Mill
Modern ball mills may use between 32 and 37 fossil fuels and electricity, account for 30 to 40% of kWh/ton of electrical energy (Worrell et al., 2013). the industry’s cash costs (Cantini et al., 2021; The power consumption of a ball mill rated 2.5 MW International Finance Corporation, 2017; Worrell et stands at 27.5 kWh/t of cement produced making the al., Energy efficiency in a cement plant is measured as a combination of two factors, viz., Thermal Energy Consumption and (2) Electrical Energy Consumption. Vertical Roller Mill: 16.50: Raw Mill Ball Mill: 23.90: Coal Mill Vertical Roller Mill: 16.28: Five Stage Preheater Clinkerisation: 17 05: Six+ Stage PreheaterCMA
احصل على السعر
Energy Efficiency Analysis of Copper Ore Ball Mill Drive
Analysis of Variant Ball Mill Drive Systems. The basic element of a ball mill is the drum, in which the milling process takes place ( Figure 1 ). The length of the drum in the analyzed mill (without the lining) is 3.6 m, and the internal diameter is 3.4 m. The mass of the drum without the grinding media is 84 Mg.The first and second laws efficiency of the CBM increased (81.8% and 20.6%) and the electrical energy consumption of CBM unit decreased (36.5 kWh/t) after modifying the ball charge pattern. Also, the results demonstrated that cement production rate increases (185–224 t/h) and the electrical consumption decreases (41.1–33.1 Energy and exergy analyses for a cement ball mill of a new
احصل على السعر
DETERMINATION OF CORRELATION BETWEEN SPECIFIC ENERGY CONSUMPTION
vibration values on the main driving motors less than 4 mm/s by periodical maintenance, the specific electrical energy consumption of the mill has reduced by 2.16% to 24.97 kWh/ton farine which corresponds to a saving of 0.55 kWh per ton of farine production. Keywords: Cement, Raw mill, Vibration, Energy, GrindingBall mill optimisation than 60 per cent of electrical energy consumption is used for grinding. In optimising the process, the grinding tools will have a significant impact on lower 29.8kWh/t, representing a ~16 per cent drop in BALL MILLS Ball mill optimisation
احصل على السعر
The energy efficiency of ball milling in comminution
Comminution represents up to 50% of the total energy consumption in the mineral production process [2]. Moreover, comminution using ball milling is highly inefficient due to heat and mechanicalKeywords: Grinding media; ball mill; comminution; Ball size distribution; wear; alloy; cast iron 1. Introduction According to data analysis by Napier-Munn [1] the comminution process consumes 1.8% of the world’s generated electricity, excluding energy used by ancillary equipment and indirect energy consumption by liners and grinding me Grinding Media in Ball Mills-A Review Preprints
احصل على السعر
Effects of Mill Speed and Air Classifier Speed on Performance of
Optimum performance of ball mill could potentially refine Blaine fineness, thereby improving the cement quality. This study investigates the effects of separator speed and mill speed on BlaineThe average electricity consumption of raw material mill dropped from 30.88 kWh/t in 2014 to 16.13 the ball mill has reached 5–6 m, dropped from 30.88 kWh/t in 2014 to 16.13 kWh/t in(PDF) A Survey and Analysis on Electricity Consumption of Raw
احصل على السعر
(PDF) Energy Efficient Ball Mill Circuit Equipment Sizing
b=70%. b= 100%. b=0%. 2. E. It should be emphasised that this increase is with respect to ~95% passing size material and not 80%. passing size (or P80) as defined in Bond’s method. screen sizesA further sampling campaign was carried out at the end of March to early April 2014. The mill was still producing scats, though less than at 78% of critical speed. The original milling circuit design for the Kroondal platinum concentrator was based on the following: > Primary milling discharge of 30% passing 75 μ m.Milling circuit optimization study for Kroondal no. 1 platinum
احصل على السعر
(PDF) Determination of correlation between specific energy consumption
Keeping the vibration values on the main driving motors less than 4 mm/s by periodical maintenance, the specific electrical energy consumption of the mill has reduced by 2.16% to 24.97 kWh/tonFill level, % mill volume: 3: 6: 10: 13: 16: 19: 23: 5. Rear view of the ball mill showing the electric motor, the torque sensor and the gear. Download : Download high-res image (236KB) Charge behaviour and power consumption in ball mills: sensitivity to mill operating conditions,Frequency domain characterization of torque in tumbling ball mills
احصل على السعر