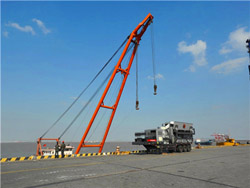
A comprehensive review on the cutting and abrasive
Among various traditional machining methods, the abrasive machining processes are the most commonly used in machining of cemented carbide. With the development of super The ball-milling process used 6-mm diameter cemented carbide balls and a cemented carbide jar. After ball milling, the leachate (containing the dissolved Co salt) Facile recycling of cemented tungsten carbide soft scrap via
احصل على السعر
Microstructure, mechanical properties, and cutting performances
Cemented carbide balls were placed in a ball-mill tank. The ball milling speed was 400 rpm and the ratio of cemented carbide balls to mixed powders was 4:1. In order to achieve high-quality milling of cemented carbide micro-lens array, the design and fabrication of the 0.5-mm diameter polycrystalline diamond (PCD) micro Structural design and fabrication of polycrystalline diamond micro ball
احصل على السعر
Micro-texture design criteria for cemented carbide ball-end
We consider the cutting performance of a cemented carbide micro-texture ball-end milling cutter as an evaluation standard. A genetic algorithm is applied to the Cemented carbide is widely used in the mold industry due to its excellent properties such as aviation, aerospace, automobile, optical, etc. [1]. Among mechanical Development of polycrystalline diamond micro end mill for
احصل على السعر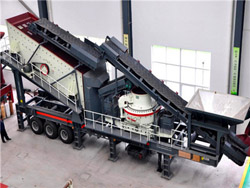
Development of polycrystalline diamond micro end mill for
Cheng et al. [6] designed and developed a PCD micro ball-end mill with 0.2 mm diameter for the realization of micro/nano free-form surface machining of hard and Planetary low temperature high energy ball mill was used for preparing the mixed powders with different particle sizes by adjusting the milling time. WC–6Co Effect of high energy ball milling on the microstructure
احصل على السعر
High-energy ball milling of WC-10Co: Effect of the milling
Table 1 gives an overview of the ball milling conditions in the cemented carbides field. Ball milling can be used for “mechanical alloying” of powders, either to form compounds (e.g. formation of tungsten carbide from WO 3 + C or from W + C by direct carburization [7]) or to reduce the particle, crystallite, and grain size of an existingWC/Co carbide tank and cylindrical balls were used for the high-energy ball milling, and the ratio of ball to material was 6:1. The speed of ball milling was 240–360 r min −1. The powder after ball milling was pressed into 21 mm × 6.5 mm × 5.5 mm samples by the compression molding method.Effect of ball-milling process in combination with the
احصل على السعر
Metals Free Full-Text WC-Based Cemented
The WC-based cemented carbides were fabricated by use of a conventional powder metallurgy route. The WC–10 wt.% Co, WC–10 wt.% HEA and WC–20 wt.% HEA powders were milled with different types of tools were used in the experiment, a diamond coated cemented carbide ball nose mill and a nano-polycrystalline diamond ball nose mill. The wear tests were performed in a 5-axis mill from Mikron HSM200uLP and the tool wear was measured in an optical 3D microscope from Alicona. The surface ofMachinability analysis of cemented carbide -A
احصل على السعر
The design and optimization of micro polycrystalline diamond ball
The micro ball end mills used to repair the micro-defects on the surface of KDP crystal were designed and optimized using FE method, and the optimized tools were fabricated. grinding combined machining of cemented carbide is analyzed, and a PCD micro end mill structure with 0° circumferential relief angle is designed to realize the With the increasing use of cemented carbide in machinery manufacturing, mining, oil exploitation, and energy transportation, a large number of cemented carbide wastes are produced. According to the chemical composition test results of the mixed powder ball mill after 12 h, the mass fraction of the bonding phase Co was adjusted to Effect of Rare Earth Oxide Addition on Regenerated Cemented Carbide
احصل على السعر
Experimental evaluation on micro-texture parameters of carbide ball
Parametric optimisation of micro-texture is important to improve the performance of cutting tool in metal cutting. In this study, the simulation models of micro-textured surface of cemented carbide are established by using ABAQUS platform, and fictitious stress distribution is analysed to select the optimum micro-texture structure. Cemented carbides cover a wide range of applications in many relevant industries, i.e. as cutting tools (turning, milling, drilling) for machining of metal components in the automotive and/or aerospace industry, as components of drill bits or road headers in the rock tools and mining area or as wear parts in wire drawing dies or punch tools.Cemented carbide microstructures: a review ScienceDirect
احصل على السعر
Micro-texture design criteria for cemented carbide ball-end
A genetic algorithm is applied to the multi-objective optimization of micro-texture parameters, and a regression analysis model of micro-texture design criteria is established. This provides a standardised reference to select standard micro-texture parameters in the design and preparation of a cemented carbide micro-texture ball-end 1. Introduction. Cemented carbide is widely used in the mold industry due to its excellent properties such as aviation, aerospace, automobile, optical, etc. [1].Among mechanical precision machining methods, micro milling is one of the most flexible technologies that is being extensively used in precision machining of cemented carbide Development of polycrystalline diamond micro end mill for
احصل على السعر
High-energy ball milling of WC-10Co: Effect of the milling
The gradient cemented carbide had the highest hardness (2169 kg/mm 2), The raw material mixture was milled for 5 h with a mass ratio of alumina balls/powder of 3:1 (the diameter of the balls is 10–30 mm) in a planetary mill (PBM 210-Nano shot-Ar-300 rpm) [13]. Dry ball-milling was done and the material uses was the milling vial Teflon.The effects of cemented carbide materials on cutting edge fracture mechanism of micro end mills in aluminum alloy 7075 machining are investigated. A series of micro milling experiments on the tool wear were conducted. The surface morphologies of micro end mills were observed, and the end teeth flank wear length and tool total cutting Effects of WC grain size and Co content on microscale wear
احصل على السعر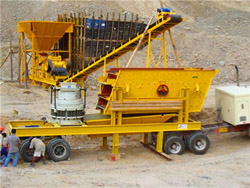
Investigation on micro milling of cemented carbide with ball
Inv estigation on micro milling of cemented carbide with ball nose and corner radius diamond coated end mills Daniel Figueiredo 1,2*,Joana Silva 3,Tiago E.F. Silv a 4,Abilio M.P. de Jesus 3,4 ,The dual-scale structure WC-6Co cemented carbide was prepared by conventional roller ball milling and vacuum sintering. • The transverse rupture strength, hardness and fracture toughness of the dual-scale structure cemented carbide reached 3077 MPa, 1570 HV 30 and 10.6 MPa•m 1/2, respectively.. The results show that the CM-2 Preparation and wear resistance of dual-scale structure cemented
احصل على السعر
Micro-texture design criteria for cemented carbide ball-end
We consider the cutting performance of a cemented carbide micro-texture ball-end milling cutter as an evaluation standard. A genetic algorithm is applied to the multi-objective optimization of micro-texture parameters, and a regression analysis model of micro-texture design criteria is established.Cemented carbide (also called WC-based hardmetal) is an old material, since it was invented in 1923 [1].However, almost after its invention, it has been used as tool materials in geo-engineering for rock drilling, mineral cutting, gas and oil drilling, tunneling projects and the like, because of its unique combination of excellent mechanical A review of cemented carbides for rock drilling: An old but
احصل على السعر
Effects of nano-alumina on mechanical properties and wear resistance
Next, WC-8Co cemented carbide balls with a diameter of φ6 ~ φ8mm were selected as the grinding body, and the mass ratio of the ball material was 10: 1. When the material was ready, the anhydrous ethanol was poured into 2/3 of During processing, the raw powders and a certain amount of cemented carbide balls were placed into a cemented carbide ball-milling tank, and pure alcohol was added as the liquid medium. Then, these mixtures were ball-milled for 30 h, 60 h, and 90 h in a high-energy planetary mill (XH-XQM-4L).Effects of Processing Parameters on the Microstructure and
احصل على السعر
Effect of particle size and high-energy ball milling time on
The effect of particle size and high-energy ball milling time on microstructure and mechanical properties of WC-10Co cemented carbides with plate-like WC grains were studied using a scanning electron microscope, x-ray diffraction and mechanical properties tests. Ciprés V C, Blomqvist A and Kaplan B 2019 Cemented Cemented tungsten carbide balls (hereafter abbreviated as WC balls) are commonly applied in grinding of wasted tool steel for reuse owing to their extraordinary surface hardness (89.5 HRA) and high density (14.5 –14.9 g/cm 3).In this study, grinding tests were conducted with WC balls on quartz ore to estimate comminution kinetics.The kinetics and efficiency of batch ball grinding with cemented
احصل على السعر