
A data-driven decision-making framework for online control
Vertical roller mill (VRM) is a large-scale grinding equipment, which is used to grind raw materials from block/granule into powder. Due to harsh production For the past three decades the vertical roller mill has emerged to be the preferred choice for grinding raw materials. With the grinding capacity of a vertical roller Review on vertical roller mill in cement industry & its
احصل على السعر
Operational parameters affecting the vertical roller mill
Vertical roller mills (VRM) have found applications mostly in cement grinding operations where they were used in raw meal and finish grinding stages and in power There are usually four kinds of VRMs in the cement production line, including raw meal mill, coal mill, Clinker Mill and cement mill, and the vertical mill occupies a large energy consumption unit. Analysis and Optimization of Grinding
احصل على السعر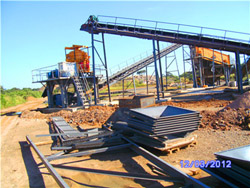
Modeling of energy consumption factors for an industrial
The raw vertical roller mill has four rollers, 3000 KW main drive, 4.8 m table diameter, 2.16 m roller diameter with 330 t/h capacity (made by LOESCHE Company This work aims to develop a soft sensor for raw meal fineness in a vertical roller mill of a cement plant. In previous research, some key indicators of the process Efficient machine learning model to predict fineness, in a vertical raw
احصل على السعر
(PDF) Design and Realization Of Roller Mill
PDF a Distributed Control System (DCS) of cement raw materials is presented for the vertical roller mill by the application of ABB's IndustrialIT. The Find, read and cite all the researchprocess condition and taking corrective action in time. In this paper, the various conventional and modern control strategies to control the process variable PROCESS CONTROL FOR CEMENT GRINDING IN
احصل على السعر
Roller Mill Based on Experimental Method mdpi-res
There are usually four kinds of VRMs in the cement production line, including raw meal mill, coal mill, Clinker Mill and cement mill, and the vertical mill Abstract. The power ingesting of a grinding process is 50-60% in the cement production power consumption. The Vertical Roller Mill (VRM) reduces the power Process control for cement grinding in Vertical Roller Mill
احصل على السعر
Effects of operational processes and equipment in palm oil mills
The characteristics of POME are largely dependent on the efficiency of the operation and process control of the mill. In Malaysia, the widely used method to extract palm oil from fresh fruit bunches (FFB) is by wet palm oil milling process (Wu et al., 2010).The unit operations used for extractions are a steriliser, a stripper, a digester, a Mill output and power consumption not only depends upon the input materials but also on the desired fineness (200 / 90 Micron) of the raw meal produced; hence a careful evaluation and targetOptimizing Raw Mills Performance ; the Materials
احصل على السعر
Vertical Raw Mill Cement Raw Mill Raw Mill In Cement Plant
Hydraulic tension system: the hydraulic cylinder produces the pressure needed for the grinding roller to tighten, and the tension rod transmits the tension force of the hydraulic cylinder.The hydraulic cylinder is equipped with a nitrogen airbag to absorb the vibration of the raw mill during operation. Nozzle ring: located between the grinding table and the An interesting historical fact is that a vertical roller mill uses the same operating principle as the pistrium or pistrinum, an antique Roman grain mill.The largest grain mills used worked aChapter Six: Some Operating Guidelines Vertical Roller Mill
احصل على السعر
Operational experience from the United States' first vertical
In 2002, Phoenix Cement Company installed the first vertical roller mill used for cement grinding in the United States, and decreased power consumption by 15 kWh/ton cement (Simmons et al., 2005Vertical Roller Mills • Do not believe screen values unless you have checked them • Continuously change Process Parameters and document results to find Optimum • Optimum is highest capacity at lowest power consumption • Be sensitive to changes of feed material and adapt parameters • Focus on Relevant Process optimization-of-vertical-raw-mill-operation.pdf Course Hero
احصل على السعر
Industrial : Optimization for the Cement Industry ABB
cement mill operations in four ways: • More consistent quality (grade). The continual monitoring of the mill loading and the adjustment of the feed and separator results in reduced variations in cement grade. This has the added benefit of a more consistent product quality. The control strategy is designed to respond to disturbances in theVertical Roller Mills. Optimization of VRM Operation Do not believe screen values unless you have checked them Continuously change Process Parameters and document results to find Optimum Optimum is highest capacity at lowest power consumption Be sensitive to changes of feed material and adapt parameters Focus on Relevant Optimization of Vertical Raw Mill Operation PDF Scribd
احصل على السعر
Verticalrawmill Pradeepkumar 130515030859 Phpapp02 PDF Mill
f1.3 The guarantee of the grinding temperature: vertical roller mill is drying and grinding system, the ground temperature is a measure of whether the normal drying operation comprehensive index. In order to ensure good drying of raw materials, the grinding of materials is less than 0.5% moisture, the general control of mill outlet temperatureA cement Vertical Roller Mill modeling based on the number of breakages. Vertical roller mills (VRM) are widely used to grind, dry, and select powders from various materials in the cement, electric power, metallurgical, chemical, and nonmetallic ore industries. For the sectors above, the VRM is a powerful and energy-intensive grinding Operational parameters affecting the vertical roller mill
احصل على السعر
Indicate Contributions from Several Radial
Operation optimization or process optimization is a critical step responsible for efficient operation of Mill. It constitutes of optimization of operation parameters like Flow, Differential Pressure, Classifier Speed, Mill Inlet & Outlet Temp, Hydraulic Pressure, equipments, control logic, PID tuning, breakdowns etc.vertical roller grinding mills for grinding: • Coal • Cement raw material • Clinker / granulated slag • Industrial minerals, and • Ores The core elements of these plants are the Loesche vertical mills for dry-grinding the above-mentioned grinding stock. Loesche has developed and built the largest and mostPROCESS OPTIMISATION FOR LOESCHE GRINDING
احصل على السعر
(PDF) Performance Evaluation of Vertical Roller
mill operation is crucial for control the s ystem and . Recent decades have proven the great effectiveness of a vertical roller mill for grinding raw materials. Its effectiveness, combinedVertical Roller Mill. Operation and Optimization Used in Cement Industry vertical mill used for pre grinding of clinker (lumps to coarse. powder) finish grinding (lumps to powder ) of coal/petcoke for kiln raw material for kiln cement, OPC or mixed slag, pure or mixed Working Principle vertical mills comprise 2-4 conical rollers which are VRM Operation and Optimization PDF Mill (Grinding)
احصل على السعر
Optimization-of-Vertical-Raw-Mill-Operation.pdf SlideShare
Optimization-of-Vertical-Raw-Mill-Operation.pdf. 1. Vertical Roller Mills • Do not believe screen values unless you have checked them • Continuously change Process Parameters and document results to find Optimum • Optimum is highest capacity at lowest power consumption • Be sensitive to changes of feed material and adapt parametersA control oriented model was then developed by Fan (1994) and Fan and Rees (1994). In 2009, coal flow and outlet temperature of mill were modelled using mass and heat balance equations for startup(PDF) Modeling and Parameter Identification of Coal Mill
احصل على السعر
Roller Mill Based on Experimental Method mdpi-res
There are usually four kinds of VRMs in the cement production line, including raw meal mill, coal mill, Clinker Mill and cement mill, and the vertical mill occupies a large energy consumption unit. Therefore, it is necessary to optimize the multi-objective parameters of the VRM in order to improve the grinding performance and reduce energyFor raw materials and cement clinker, the vertical roller mill is an excellent grinding solution because of the relatively lower cost of installation, ease of operation and maintenance, energy efficiency and product quality. Further, our vertical roller mill solution for cement grinding has an ability to dry, grind and separate within a singleVertical Roller Mills FLSmidth
احصل على السعر
Modeling of energy consumption factors for an industrial
The raw vertical roller mill has four rollers, 3000 KW main drive, 4.8 m table diameter, 2.16 m roller diameter with 330 t/h capacity (made by LOESCHE Company from Germany).Introduction. Vertical roller mill (VRM) is a type of heavy-duty and energy-intensive grinding equipment for many industries, such as cement, steel and chemical industries. It is used to grind slag, nonmetallic ore and other block and granular raw materials into required powder materials. The fine powders can be used as raw materials A data-driven decision-making framework for online control of vertical
احصل على السعر