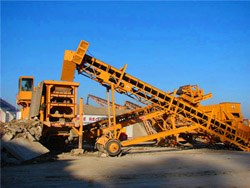
An innovative approach for determining the grinding media system
The dry grinding experiment was operated in the ball mill (Φ460 × 600 mm) with steel ball as grinding media at mill speed 47 r/min, space-filling factor φ 30%, and The performance of grinding media in a ball mill is measured in terms of wear rate, which is a function of the media composition, hardness, phase structure, and A Review of the Grinding Media in Ball Mills for Mineral
احصل على السعر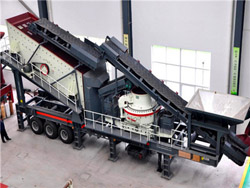
Tailoring ball mill feed size distribution for the production of
This makes feed tailoring in ball milling an interesting parameter to investigate with the aim of maximising the desired mill product. To that end, batch tests In this paper, different from the traditional two-input-two-output model of the ball mill grinding process, a three-input-three-output system considering the influence Process Control of Ball Mill Based on MPC-DO Hindawi
احصل على السعر
Intelligent optimal control system for ball mill grinding
1 Introduction The grinding process is a run-of-mine ore size reduction operation used in the mineral industry to liberate the valu- able minerals to be recovered In ball mills, steel balls or hard pebbles to break particle based on impact and attrition. A rotating mill charged with media and ore is lifted against the inside perimeter. Some of the media falls and impacts the ore particles at AMIT 135: Lesson 7 Ball Mills & Circuits Mining
احصل على السعر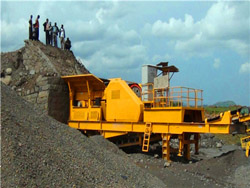
Ball Mill an overview ScienceDirect Topics
Ball mills give a controlled final grind and produce flotation feed of a uniform size. Ball mills tumble iron or steel balls with the ore. The balls are initially 5–10 cm diameter but Ball-milling is a low-cost and green technology that offers mechanical actions (shear, friction, collision, and impact) to modify and reduce starch to nanoscale Ball-milling: A sustainable and green approach for starch
احصل على السعر
Ball Mill an overview ScienceDirect Topics
where d b.max is the maximum size of feed (mm); σ is compression strength (MPa); E is modulus of elasticity (MPa); ρb is density of material of balls (kg/m 3); D is inner diameter of the mill body (m).. Generally, a maximum allowed ball size is situated in the range from D /18 to D/24.. The degree of filling the mill with balls also influences productivity of the mill The grinding process in the ball mill is due to the centrifugal force induced by the mill on the balls. This force depends on the weight of the balls and the ball mill rotational speed. At low speeds, the Finite Element and Multibody Dynamics Analysis
احصل على السعر
Control of a closed dry grinding circuit with ball mills using
Inapakurthi et al. (2020) used recurrent neural networks to model a grinding circuit in lead-zinc ore beneficiation process, consisting of a rod mill, ball mill, two hydro-cyclones and two water sumps (primary and secondary). The system consists of three MV (ore feed rate and water supply in the sumps) and three CV (throughput, % solids A ball mill is a type of grinder widely utilized in the process of mechanochemical catalytic degradation. It consists of one or more rotating cylinders partially filled with grinding balls (made(PDF) Grinding in Ball Mills: Modeling and Process Control
احصل على السعر
Mechanistic modeling and simulation of grinding iron ore pellet feed
Various approaches have been used over the years to describe quantitatively ball milling, with different levels of success.The present work presents the application and validation of a mechanistic model to describe ball milling of iron ore pellet feed. The approach started by estimating selected parameters describing the ore Ball mills find applications across many disciplines, from materials research to chemical analysis and even biological research [78,79,80]. Ball milling is a process that utilizes mechanical forces, such as those generated by the rotating jar of a ball mill, to break up the material into smaller pieces and mix them together .Producing Metal Powder from Machining Chips Using Ball
احصل على السعر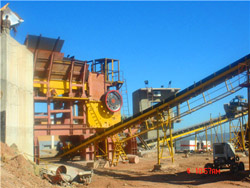
行星式球磨仪PM100--德国RETSCH(莱驰)研磨仪粉碎仪
Download. The Planetary Ball Mill PM 100 is a powerful benchtop model with a single grinding station and an easy-to-use counterweight which compensates masses up to 8 kg. It allows for grinding up to 220 ml sample material per batch. The extremely high centrifugal forces of Planetary Ball Mills result in very high pulverization energy andIs based on assumptions: 1) Optimum ball sizes are related to particle sizes according to the following equation: d1/d2 = (D1/D2)1.7. d = particle diameter. D = ball diameter. 2) Particle size distribution along the mill axis can be expressed as a function of %. residue at particle size di:1 Ball Mills 1 PDF Mill (Grinding) Gases Scribd
احصل على السعر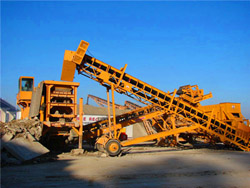
AMIT 135: Lesson 7 Ball Mills & Circuits Mining Mill
Ball Mill Design Parameters. Size rated as diameter x length. Feed System. One hopper feed; Diameter 40 100 cm at 30 ° to 60 ° Top of feed hopper at least 1.5 meter above the center line of the mill.The present study investigates the propensity of predicting ore grindability characteristics and varying pulp densities through acoustic measurements on the Magotteaux ball mill. Specifically, the grinding behaviour of two different mill feeds (model quartz and iron ore) together with solid loadings (50, 57, and 67 wt% solids) were Predicting mill feed grind characteristics through acoustic
احصل على السعر
BALL MILLS Ball mill optimisation holzinger
BALL MILLS 1 FEBRUARY 2021 INTERNATIONAL CEMENT REVIEW T here are currently several energy-efficient grinding systems available for the cement and mineral industry, including vertical roller mills (VRM), high-pressure grinding units (HPGR) or simple roller presses, as well as the most traditional type of installation: ball mills, Fig. 1 shows the proposed modelling framework which consisted of three closely integrated models: a DEM model to simulate the dynamics of particles and generate information such as ball-particle-mill contact forces, ball/particle-mill collisions and power draw; an AE model to convert ball/particle-wall collisions to AE signals; and a CNN model Prediction of ball milling performance by a convolutional
احصل على السعر
17 Signs of Problems with Ball Mills: Quickly Remove Hidden Troubles
High temperature of the ball mill will affact the efficiency. 3 For every 1% increase in moisture, the output of the ball mill will be reduced by 8% -10%. 4 when the moisture is greater than 5%, the ball mill will be unable to perform the grinding operation. 5. The bearing of the ball mill is overheated and the motor is overloaded.Abstract and Figures. In this paper a new digital energy meter is being evaluated as a means of measuring the energy required to grind ore in the Bond mill and to test if the results are(PDF) Measurement of electrical energy consumption in a Bond ball mill
احصل على السعر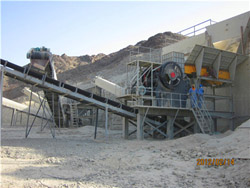
AG/SAG mill acoustic emissions characterisation under different
The combination of two or more parameters also produced interesting results with blends of steel balls and rock reducing the mill noise considerably relative to steel ball only, by dampening the noise intensity, which is akin to rock, steel balls, and water system. 3. An increase in the mill speed generally produced higher acoustic emissions.Comchambered with the design of Φ 3.5 × 13m three-chamber ball mill, the design process of ball mill is described in detail. General arrangement of the mill Filling rate of grinding body in each(PDF) Design of Three-chamber Ball Mill ResearchGate
احصل على السعر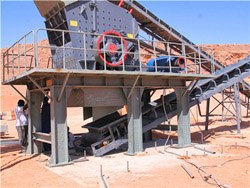
Closed circuit ball mill Basics revisited Request PDF
For a closed circuit ball mill flowsheet as represented in Figure 2, a simplified relationship (Equation 1) for relative capacity at different circulating load and classification efficiencies wasProcessing in planetary ball mills is well suited to a large number of applications because they are easy to operate and versatile, grinding faster than other mills. Research related to planetary mills are mainly about the process evaluation, and there are few studies on the mechanical design of such equipment. This paper describes the Machines Free Full-Text Planetary Mill with Friction
احصل على السعر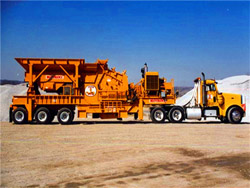
Ball Mills Ball Mill Ball Milling Orbis Machinery
Steel Ball Mills & Lined Ball Mills. Particle size reduction of materials in a ball mill with the presence of metallic balls or other media dates back to the late 1800’s. The basic construction of a ball mill is a cylindrical container with journals at its axis. The cylinder is filled with grinding media (ceramic or metallic balls or rods
احصل على السعر