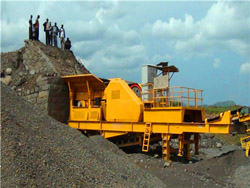
Indian Cement Industry Analysis IBEF
India's cement productionCement is the essential “glue” in concrete, a fundamental building material for society’s infrastructure around the world. The cement manufacturing process is Green cement production in India: prioritization and
احصل على السعر
Indian Cement Industry: A Key Player in the Circular Economy of India
Indian cement industry being one of the second largest cement production after China with an installed capacity of 509 MTPA (million tonnes per Annum) in 2018 is Type of Process. There are mainly two types of Cement Manufacturing process: Wet Process; Dry Process; Wet Process. Under wet process type, the raw Cement BUREAU OF ENERGY EFFICIENCY, Government of India
احصل على السعر
Indian Cement Industry, Top Cement Companies in India- IBEF
Nearly 32% of India's cementIndia as the second largest cement producer in the world needs to focus on the sustainability of cement manufacturing. The cement manufacturing is a high energy Readiness self-assessment of cement industry for sustainable
احصل على السعر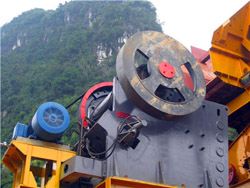
India: cement production volume 2022 Statista
Production volume of cement in India from financial year 2008 to 2019 with a forecast until 2022 (in million metric tons) [Graph], India Brand Equity Foundation, January 17, 2023. [Online].There are four stages in the manufacture of portland cement: (1) crushing and grinding the raw materials, (2) blending the materials in the correct proportions, (3) burning the prepared mix in a kiln, and (4) grinding the burned product, known as “ clinker,” together with some 5 percent of gypsum (to control the time of set of the cement). The three processes of Cement Extraction, Processing, Manufacturing Britannica
احصل على السعر
Decarbonising cement: One of the biggest challenges in the
This process releases CO2 as a byproduct, known as process emissions, contributing to a significant portion of the industry's carbon footprint. Clinker, responsible for approximately 90% of emissions in cement production, is a primary focus of the industry's decarbonisation efforts. Cement manufacturers can explore alternatives such as fly ashAccording to the findings, India is the second largest cement producer after China, with an installed capacity of 537 million tonnes and around 7.1 percent of the world’s production, up from 337.32 million tonnes in 2019. NOx, SOx, CO, CO2, H2S, VOCs, dioxins, furans, and particulate matter are all common air pollutants from cement A systematic review on the impact of cement industries on
احصل على السعر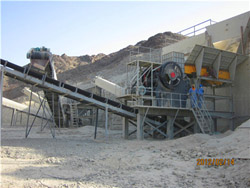
Environmental Impact Assessment of Cement Industry my
EIA stands for Environmental Impact Assessment. UNEP (United Nations Environment Programme) defines Environmental Impact Assessment (EIA) as a tool used to identify the environmental, social and economic impacts of a project prior to decision-making. Today we are going to look at one of the most important processes of EIA for the The standard bag of cement as distributed in India is commonly 50 kg or 112 .5 lbs. 2. Wet Process of Manufacturing of Cement. It is considered a better and convenient process for the manufacture of cement, especially where limestone of soft variety is available in abundance.Cement Manufacturing Process: What is Cement made of.
احصل على السعر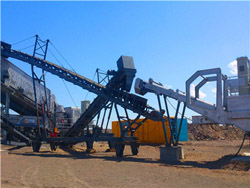
(PDF) Cement Manufacturing ResearchGate
Table 1. Raw materials are used to produce the main cement elements (Mohsen, 2015) • Quarry The process of obtaining raw materials for cement manufacturing involves mining and quarrying naturalAccording to the ndings, India is the second largest cement producer after China, with an installed capacity of 537 million tonnes and around 7.1 percent of the world’s production, up from 337.32 million tonnes in 2019. NOx, SOx, CO,CO 2, H 2 S, VOCs, dioxins, furans, and particulate matter are all common air pollutants from cementA systematic review on the impact of cement industries
احصل على السعر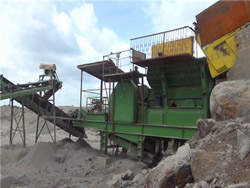
(PDF) A sustainability assessment framework for cement industry
The empirical study of the Indian cement industry identifies 52 KPIs (17 social, production process some water quantity is lost due to consumption, evaporation or leakage (i.e. water.India is the second major producer of cement in the world after China (CMA 2018) and third largest emitter of carbon dioxide after USA and China (Mishra et al. 2015).The per capita cement consumption in India is about 190 kg against world’s average consumption of 350 kg (IBEF 2016).The cement production in India in 2014 was 275 MT Composite Cement: A Sustainable Binding Material for Real
احصل على السعر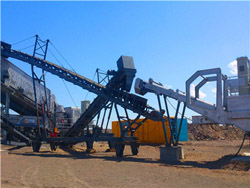
Sustainable transition towards biomass-based cement
Policy intervention points to achieve a sustainable transition are proposed. Cement manufacturing is a hard-to-abate industrial sector that accounts for 5–8% of global anthropogenic emissions. Approximately 80–90% of these emissions occur during limestone calcination and fuel combustion processes. Decarbonising these two emission and India’s per capita consumption is rough to the tune of 200-225 KG. It is relatively less compared to the global average, which is around ~ 500 KG. In other major emerging economies like China, the per capita consumption is even higher at around ~ 1000 KG. In the foreseeable future, the cement industry is expected to grow at a remarkable paceThe India Watch
احصل على السعر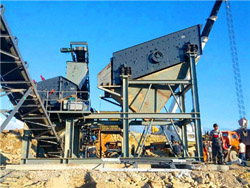
The Cement Manufacturing Process Environmental and Social
The Cement Manufacturing Process Environmental and Social Impact. The cement industry is among India’s most polluting industries. Image courtesy: businesstoday.in. The Indian cement industry is the second-largest producer of cement globally. In the financial year 2020, the Indian cement industry had a turnover of Rs The overall CO 2 emissions from cement manufacturing, including process and energy-related emissions has a significant interest. Actually, much of the relevant evidence only covers process pollution. CO 2 pollution control solutions for the cement industry are also discussed. In 1994, the projected gross carbon emissions from cementIntroductory Chapter: Cement Industry IntechOpen
احصل على السعر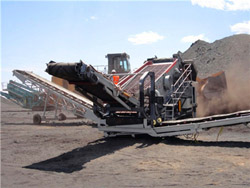
Pyroprocessing and Kiln Operation Indian Cement Review
January 16, 2023. By. admin. Dr SB Hegde, Professor, Jain University, Bangalore, talks about pyroprocessing and the role of preheater, rotary kiln and clinker cooler in the cement manufacturing process. In the concluding part of the two-part series, we will learn more about the various factors aiding pyroprocessing. False Air in Pyro Processing.The Indian Cement Industry presents its multi-faceted approach to manufacturing environmentally compatible cement a.k.a. Green Cement as it races against time to minimise carbon footprint of cement production and accelerate the nation’s efforts towards achieving Net Zero deadline. Cement production is one of the highest-emitting An Open and Shut Indian Cement Review
احصل على السعر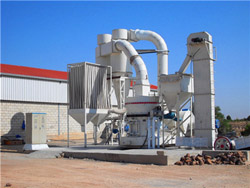
(PDF) A Review Article on Manufacturing Process of Cement
The production process of cement involves burning of limestone and clay together in a rotary kiln at a temperature of about 1,450°C (Gaharwar, Gaurav, Singh, Singh, & Gariya, 2016). This might beThese brick-making machines are available in a variety of sizes and capacities. Bricks may be made at a rate of 1,000 to 10,000 per hour on a standard machine. This equipment costs anywhere between 10-13 lakh. Bricks can be sold for between 30-40 lakh and 5 lakh bricks.How To Start Cement Bricks Manufacturing in India 2023
احصل على السعر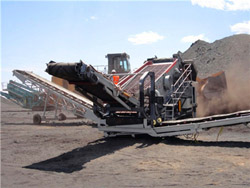
Moving Towards Net-Zero Indian Cement Review
The 3-in-1 event comprising Indian Cement Review (ICR) Conference, Awards and Cement EXPO 2023 scheduled on 14-15th December 2023 at Manekshaw Centre in Delhi is expected to attract cement industry captains, plant heads, over 100 exhibitors and more than 5,000 quality visitors.Cement is one of the key essentials in the construction sector and forms the backbone of a nation’s economy. The total world cement production is around 4.1 billion tonnes in 2019, with India being the second-largest cement producer after China [1, 2].The current annual production of the Indian cement industry is 334.48 million tonnes as of Recent Progress in Refuse Derived Fuel (RDF) Co-processing in Cement
احصل على السعر