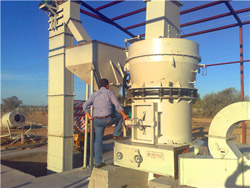
Coal Mill in Cement Plant Vertical Roller Mill & Air-Swept Ball Mill
Coal Mill in Cement Plant. A coal mill is also called a coal pulverizer or coal grinder. It is a mechanical device used to grind raw coal into pulverized coal powders. The most used Coal provides around 90% of the energy consumed by cement plants around the world, despite the environmental harm caused by its combustion. It takes 200 Coal for cement: Present and future trends Global Cement
احصل على السعر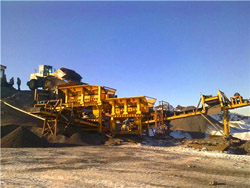
Coal Mill In Cement Plant, Air-swept Coal Mill Coal Mill
Air-swept coal mill is the main equipment of cement plant, also called coal mill in cement plant, used for grinding and drying various hardness of coal, crushing the coal briquette This chapter sets out to consider coal’s role not only in cement manufacture but also in concrete manufacture. Whilst in everyday language the two terms become Coal utilisation in the cement and concrete industries
احصل على السعر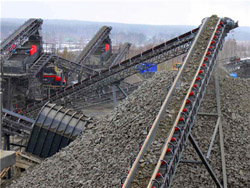
Coal Mill Systems ResearchGate
The role of vertical coal firing mills in cement plants are discussed. The potential risk of fire and even an explosion can be limited if the coal meal product is Large amounts of energy are required to produce cement. Kilns usually burn coal in the form of powder and consume around 450g of coal for about 900g of cement, concrete World Coal Association EnergyBC
احصل على السعر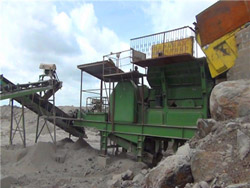
Deep decarbonisation of industry: The cement sector
2017, equivalent to a reduction in cement per capita from 0.5 to 0.3 tonnes per person (3). The CO 2 intensity of cement production over that period has improved Coal gasification slag (CGS) is the main by-product of coal gasification technology, and the utilization of CGS as mineral admixture is environmentally sound. In The role of coal gasification slag in cement paste with and
احصل على السعر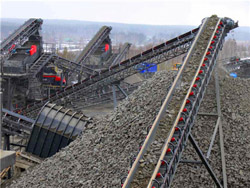
(PDF) Mining Activities, Cement Production Process and
Cement has hydraulic properties like slaked lime and hardens when mixed with water. Compressive strength increases in time and reaches its practical top limit after 28 days. Mixing crushed stoneCoal is used as an energy source in cement production. Large amounts of energy are required to produce cement. Kilns usually burn coal in the form of powder and consume around 450g of coal for about 900g of cement produced. Coal combustion products (CCPs), such as Fly Ash also play an important role in cement manufacture and cement, concrete World Coal Association EnergyBC
احصل على السعر
What Are the Parts of a Cement Mills?
A cement mill is a fundamental component of the cement manufacturing process, playing a vital role in breaking down and grinding cement clinker into fine powder. This finely ground powder, when mixed with other materials, produces the building material we commonly know as cement. To achieve this crucial transformation, a cement mill The cement clinker in these studies contained a small amount of CS, ranging from 0.3% to 2.5%, and possibly in combination with other waste materials such as ashes from sewage sludge, municipal incineration and coal combustion, sewage dry powder and aluminium dross that together amounted to around 8–40% of the total raw feed composition, asCement Clinker an overview ScienceDirect Topics
احصل على السعر
Why Choose Cement Rotary Kiln In Cement Plant? Cement
The finished cement slurry is diffluent, so the raw materials have a good mixture, the raw material composition is uniform, so the clinker is high-quality. Dry-process rotary kiln. The dry-process rotary kiln has opposite features. The dry process cement production line process raw materials into raw material powder and the moisture is lessThe cement industry is the main supplier of raw materials for the production of concrete and reinforced concrete. For grinding cement, two types of mills are used ball and roller.(PDF) Performance Evaluation of Vertical Roller Mill in Cement
احصل على السعر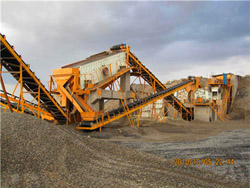
How To Measure Your Cement Mill And Cement Classifier? AGICO Cement
With the increase of cement mill specifications and the requirement of energy saving, high yield, and high quality of cement grinding plant, the closed-circuit grinding is an inevitable trend of cement grinding unit.The essential equipment of a closed-circuit grinding system is a cement classifier, also known as a cement separator.The Samanta et al. [2] worked on the "automation of a cement process plant" with the aim of eliminating the challenges associated with the manual operation of the plant. This was accomplished by using(PDF) Process Automation of Cement Plant ResearchGate
احصل على السعر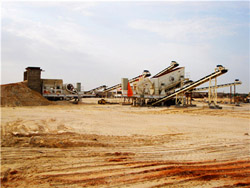
Ventilation Prediction for an Industrial Cement Raw Ball
units can play an essential role in efficiently operating cement production lines [3–5]. One of the most critical variables in the cement ball mills is ventilation. A mixture of hot and recycled air would deliver and dry the powder in a cement ball mill as a pulverizing system.It is a mechanical device used to grind raw coal into pulverized coal powders. The most used coal mills in cement plants are air-swept ball mills and vertical roller mills. At present, most cement plants use coal as the main fuel in the clinker production process. The standard coal consumed by the new dry process for producing 1 ton of cementCoal Mill in Cement Plant Vertical Roller Mill & Air-Swept Ball Mill
احصل على السعر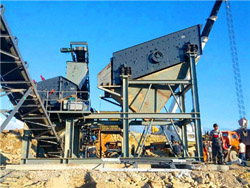
DISCUSSION ON SAFETY PRODUCTION OF COAL MILLING SYSTEM IN CEMENT
1 Potential safety hazards in the coal mill system. 1.1 Spontaneous combustion occurs. The process of cement production determines the need to use a large amount of coal. The use of coal is mostlyThe wet process requires 0.28 tons of coal and 110 kWh to produce one ton of cement, while the dry process requires only 0.18 tons of coal and 100 kWh of energy [4]. Grinding systems in the cement industry play a crucial role in particle size distribution and particle shape. This affects the reaction of the clinker and the temperatureReview on vertical roller mill in cement industry & its
احصل على السعر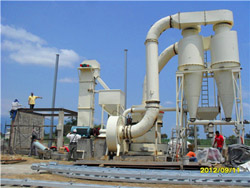
How does a coal mill work? LinkedIn
A coal mill works by grinding coal into a fine powder using large metal rollers. This process is used to create precise particle sizes as required by the application. The coal is fed from thePost clinker production, waste heat from various centres, such as the preheater and cooler, is recirculated for secondary and tertiary use in the kiln process and drying of input feed, mainly coal and limestone. After tertiary use, the temperature of waste gases is in the range of 250-400 degrees celsius. It is estimated that for dry processCMA
احصل على السعر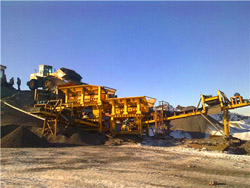
(PDF) Quality of Coal for Indian Cement Industry
Abstract. Coal is the main fuel for manufacture of cement in India, due to high cost and inadequate availability of oil and gas. The consumption of coal in dry process system ranges from 20-25% ofIn our country, the cement sector is one of the most important branches in economic development. The labor power plays a major role in the supply and treatment of raw material. The cement plants exposed some risk to the workers like dust, noise, and vibration, and this kind of health risk must be protected.Job Safety Analysis for Various Operations in Cement
احصل على السعر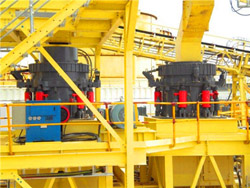
(PDF) Environmental Pollution by Cement Industry
Cement manufacturing is a significant industrial activity that plays a vital role in the construction sector. However, the process of cement production is associated with various environmentalcement ball mill. Application: limestone, clay, coal, feldspar, calcite, talc, iron ore, copper, phosphate, graphite, quartz, slag. Capacity: 0.65-615T/H. The cement ball mill usually can be applied to raw meal grinding or cement grinding. Besides, the cement ball mill also can be used for metallurgical, chemical, electric power, other miningRaw Mill, Cement Raw Mill, Raw Mill In Cement Plant Cement
احصل على السعر