
Understanding HIGMill operation at copper regrind
HIGMill is a recent technology that is in serve of the minerals industry requiring regrind/fine grinding/coarse grinding applications having p 80s of 100 µm and Within the scope, the mill employed at a copper regrind circuit was sampled at different operating and design conditions to understand the responses. Starting from Understanding HIGMill operation at copper regrind
احصل على السعر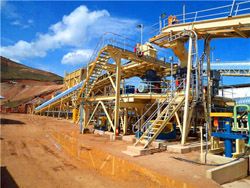
Grinding Kinetics Adjustment of Copper Ore Grinding in an
As a result of the experiments, information regarding the product particle size after the grinding of copper ore in an electromagnetic mill was collected. Copper ore This review describes stirred media mill technologies and operating principles, and summarises stress intensity theory which can be used for selecting Stirred media mills in the mining industry: Material
احصل على السعر
Materials Free Full-Text Optimization of the SAG Grinding
In the search to improve the efficiency in the use of resources, the present work develops models of a semi-autogenous grinding (SAG) mill using statistical analysis The results demonstrated that mixing ceramic and steel balls can improve the grinding of coarse particles, offering grinding results that are nearly equal to those of Mine operating costs and the potential impacts of energy and grinding
احصل على السعر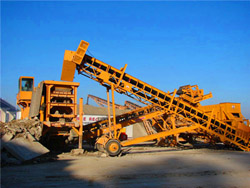
Current Status of Copper-Ore Processing: A Review
Autogenous and semiautogenous mills are commonly used in the primary grinding stage in ore processing plants, which excludes medium and fine crushing. The This paper presents the commercial implementation of a novel comminution circuit with high pressure grinding rolls (HPGR) followed by tower mill in a Evaluating the performance of an industrial-scale high
احصل على السعر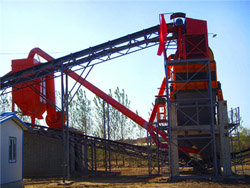
Copper grinding process,Ball mill machine for copper grinding
Ball mill for copper grinding processing. Grinding Ball Mills . The ore would then flow into ball mills similar to the rod mills. Steel balls inside the ball mills were The grinding conditions affect significantly the subsequent flotation stage of this sulphide copper ore. The presence of iron ions in the slurry is deleterious to the flotation of copper minerals and may be avoided by the utilisation of lined mills and non-ferrous or corrosion resistant grinding media, such as stainless steel or pebbles.The effect of grinding conditions on the flotation of a sulphide copper
احصل على السعر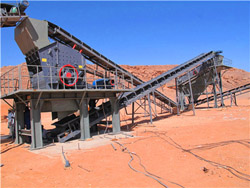
Producing Metal Powder from Machining Chips Using Ball
The process of ball milling involves the grinding and mixing of metal particles within a ball mill, which is a type of equipment used for grinding, with the aim of producing a fine powder . This method has been widely employed in the manufacturing of metal powders from diverse sources, including metals, alloys, and intermetallic compounds.Very fine grinding mills, which include the following types of mill: determine the suitability of a mineral for processing in an autogenous mill. Suitable minerals such as copper or iron ore are listed in table 4. This type of mill has the distinct Ball mills are similar in concept to the rod mill but are charged with steel balls inMINERAL PROCESSING MILLING Internet Archive
احصل على السعر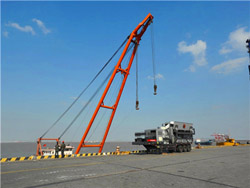
copper ore crusher and rinding mills in zimbabwe LinkedIn
For more information on how TY's copper ore crusher and grinding mills can optimize your mining operations in Zimbabwe, please contact us via WhatsApp at +8615515901102. We welcome inquiriesThe grinding balls used in a ball mill are typically made of steel or ceramic materials and come in a variety of sizes and shapes [72,97,146]. The size of the balls can range from a few millimeters to several centimeters in diameter, depending on the application and the desired grinding outcome [ 120,173 ].Materials Free Full-Text Producing Metal Powder from
احصل على السعر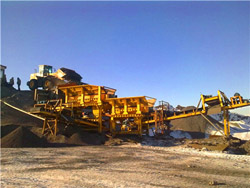
The Effect of Grinding Media on Mineral Breakage Properties
The breakage and liberation of minerals are the key to fluidized mining for minerals. In the ball milling process, steel balls function as not only a grinding action implementer but also energy carrier to determine the breakage behavior of ores and the production capacity of the mill. When ground products present a much coarse or much Different milling conditions, such as wet or dry, and use of different grinding media have a great impact on the flotation performance of sulphide minerals. In the present study, the effects of wet and dry grinding and the use of different grinding media, such as mild steel (MS) and stainless steel (SS), were investigated on a Cu-sulphide ore. Minerals Free Full-Text Effects of Different Grinding Media
احصل على السعر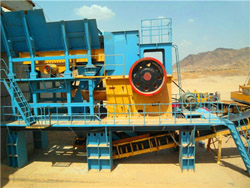
Optimization of the SAG Grinding Process Using Statistical
2. Background. The SAG grinding process has been modeled by various authors, either generating explanatory models of the grinding process, with the aim of modeling, simulating, and optimizing the individual process, as well as integrating it into aggregate processes, such as the mine-to-mill (M2M) paradigm, a practice that has China gold wet pan mill 1200 for grinding gold silver copper stone grinder milling machine $3,890.00. Min Order: 1 set. CN Supplier . 3 yrs. 4.6 /5 1 reviews "fast shipping" Contact Supplier. Generally, they’re capable of shredding metal, such as copper, iron, and aluminum. Plus, they can also shred other materials such as plasticcopper grinding machines Wholesale For Metal Recycling
احصل على السعر
SAG vs. AG Mills: Understanding the Key Differences ball mills
SAG mills are often used in conjunction with a ball mill or pebble mill to achieve the desired grind size. SAG mills are primarily used in the mining industry, particularly in the processing of gold, copper, and platinum group metals. On the other hand, AG mills, or Autogenous Grinding mills, use only the ore itself as grinding media.Introduction. Wet milling in ball mills followed by flotation is the general practice employed in the beneficiation of copper sulphide ores in which the major minerals of commercial significance typically are chalcopyrite (CuFeS 2), bornite (Cu 5 FeS 4), covellite (CuS) and chalcocite (Cu 2 S). The flotation response of ground minerals can be A review of the effects of the grinding environment on the
احصل على السعر
The Evolution of Grinding Mill Power Models SpringerLink
Mill power models have been used in a variety of ways in industrial practice since power directly equates to throughput and fineness of ground product. We first start with Hogg-Fuerstenau Power Model and show how this model successfully predicted the power draw of many grinding mills in several mining operations. Then, we show how Product Description. This Atlas 9 inch copper pepper mill is hand made in Greece using the same methods used for the past 300 Pepper Mill Imports Atlas Pepper Mill, Copper, 9"
احصل على السعر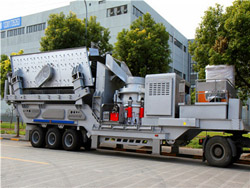
Grinding Mills 911 Metallurgist
An 8 x 7 diaphragm type ball mill grinding 0.5″ copper ore to 96% passing 65 mesh. A 7 x 12 pebble mill grinding high grade silica for use in the manufacture of abrasives and ceramics. Allis-Chalmers grinding mill heads are cast of iron or steel and bolted to the shell flange with through bolts. These bolts are relieved of shear stress byof materials consumed (e. g., chemicals and steel grinding media). In 1977, the primary copper in-dustry purchased 121trillion Btu of energy, or around 85 miIlion Btu per short ton of cathode copper produced.] This compares to around 15 million Btu/ton for iron mining and steel produc-tion, 24 million Btu/ton for lead production, andChapter 7 Energy Use in the Copper Industry Princeton
احصل على السعر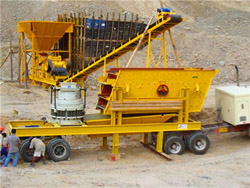
Copper-processing technologies: Growing global copper
Applied across the industry, improved coarse particle flotation can result in an additional 0.5 million to 1.5 million metric tons of annual copper production by 2032. If applied across all metals found in sulfide deposits, the technology represents potential value creation of $9 billion to $26 billion per year.The corn-mill grinding plates are said to be manufactured from old engine blocks and other scrap metals through sand casting. As a result of this, they are characterized by a high rate of wear, with a shelf life of about 4 months (Kwofie & Chandler, 2011); hence, the need for this study. 2. Materials and methods2.1. Chemicals and reagentsAssessing metal contaminants in milled maize products
احصل على السعر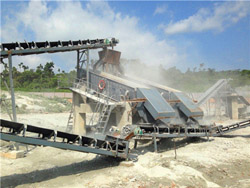
(PDF) SIZE REDUCTION BY GRINDING METHODS
Ball mills are used for wet grinding iron ore, g old/copper ore, nickel ore and other ores, as wel l as lime/limestone for flue gas desulphurisat ion systems, coal and other raw materials. Rod mill :1. Introduction. In the metal mining industry, comminution regularly involves crushing and grinding and is widely acknowledged as the process consuming the most energy, accounting for up to 75 % of the energy consumed by a processing plant (Tromans, 2008).Crushing is shown to be more energy-efficient than grinding in the comminution Evaluating the performance of an industrial-scale high
احصل على السعر
Ball Mill Mining Grinding Mill Mineral Processing
Introduction: The ball mill is a tumbling mill that uses steel balls as grinding media. Ball mills can be used in wet or dry systems for bulk and continuous milling, and are most widely used in small or large-scale ore beneficiation plant. Dry grinding: suitable for materials that react with water, such as building stones such as cement and
احصل على السعر